In the dynamic world of airport operations, the efficiency and reliability of equipment hinge on the performance of actuators. Actuators, the unsung heroes of mechanical systems, come in various types, each designed to meet specific operational demands. Understanding the types of actuators is crucial for airport managers, engineers, and procurement professionals aiming to optimize their infrastructure and ensure seamless operations. In this comprehensive guide, we will delve deep into the diverse types of actuators, exploring their features, applications, and how they contribute to the smooth functioning of airport equipment.
Electric Actuators: The Epitome of Precision and Control
Electric actuators stand at the forefront when it comes to precision, flexibility, and ease of integration. These types of actuators convert electrical energy into mechanical motion, enabling precise control over the movement of various components in airport equipment.
Working Principle
Electric actuators operate on the principle of electromechanical conversion. A motor, often an AC or DC motor, serves as the power source. When an electrical signal is sent to the actuator, the motor starts to rotate. This rotational motion is then transformed into linear or rotary motion through a series of components such as gears, screws, or belts. For instance, in a linear electric actuator, the motor's rotation is converted into a straight - line motion via a screw - nut mechanism. The motor rotates the screw, and the nut, which is connected to the load (such as a valve or a gate), moves along the screw, providing controlled linear movement.
Sub - types of Electric Actuators
Linear Electric Actuators
- Linear electric actuators are designed to produce a straight - line motion. In airport baggage handling systems, these types of actuators play a vital role. They are used to move conveyor belts, guiding luggage from check - in counters to aircraft cargo holds. The precise linear movement ensures that bags are transported smoothly and accurately, reducing the risk of damage. For example, when a bag needs to be diverted to a different conveyor line for inspection, a linear electric actuator quickly and precisely adjusts the position of the diverting mechanism.
- In addition, in airport passenger boarding bridges, linear electric actuators are used to extend and retract the bridge to connect with the aircraft. The ability to control the linear movement with high accuracy ensures a secure and seamless connection, facilitating the safe transfer of passengers.
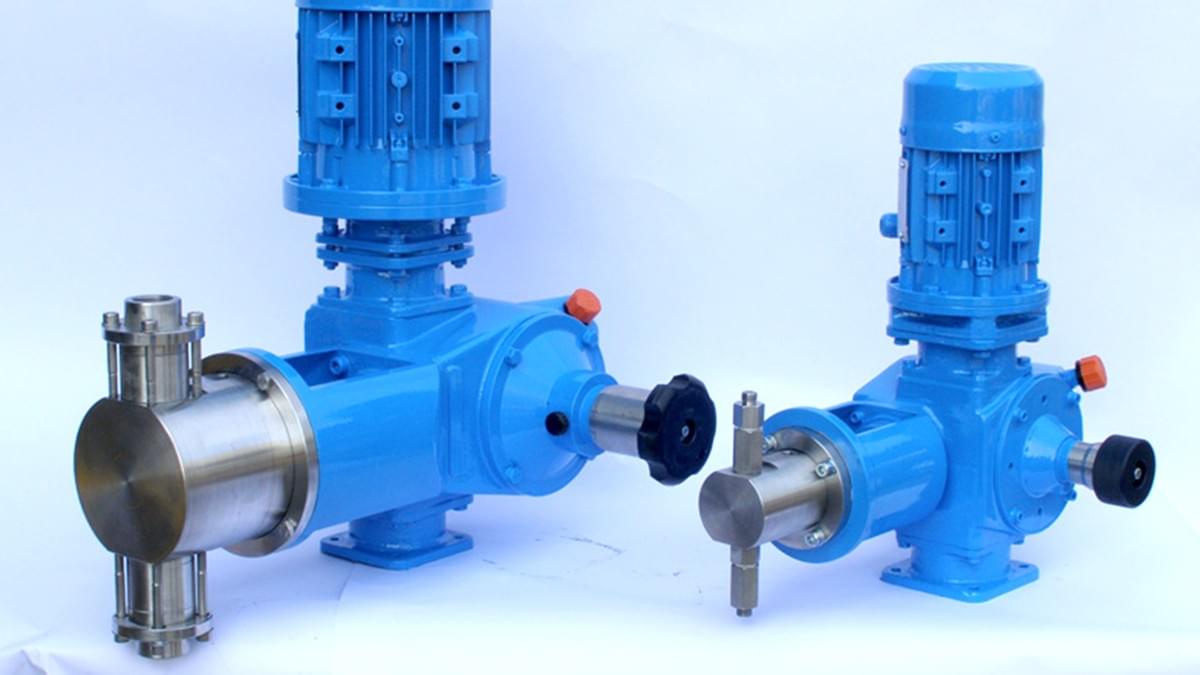
- Rotary electric actuators, as the name suggests, generate rotational motion. These types of actuators are commonly used in airport gate systems. The gates that control the entry and exit of aircraft onto the runway are often operated by rotary electric actuators. The actuator rotates the gate mechanism, allowing it to open and close smoothly and accurately. This precise control is essential for maintaining the flow of aircraft traffic and ensuring safety on the runway.
- In fueling systems at airports, rotary electric actuators are used to control the valves that regulate the flow of fuel. The accurate rotational movement of the actuator ensures that the correct amount of fuel is delivered to the aircraft, preventing over - fueling or under - fueling, which can have serious safety implications.
Advantages in Airport Applications
- Precision: Electric actuators can achieve extremely high levels of precision. With advanced control systems, they can position components with an accuracy of a fraction of a millimeter. This precision is critical in airport equipment where even the slightest deviation can lead to operational disruptions or safety hazards.
- Remote Control: These types of actuators can be easily integrated with control systems, allowing for remote operation. Airport operators can control the actuators from a central control room, enabling real - time adjustments and monitoring of equipment. For example, in a large airport with multiple baggage handling lines, operators can remotely control the actuators to optimize the flow of luggage, responding quickly to changes in passenger traffic.
- Energy Efficiency: Modern electric actuators are designed to be highly energy - efficient. They consume less power compared to some other types of actuators, which is not only beneficial for reducing operational costs but also aligns with the growing focus on sustainability in the aviation industry.
Pneumatic Actuators: Harnessing the Power of Compressed Air
Pneumatic actuators are another important category among the various types of actuators. These actuators use compressed air as the power source to generate mechanical motion.
How They Work
Pneumatic actuators consist of a cylinder and a piston. Compressed air is supplied to the cylinder, which exerts pressure on the piston. This pressure causes the piston to move, generating linear or rotary motion depending on the design of the actuator. When the air pressure is released, a spring or the pressure of air on the other side of the piston returns the actuator to its original position. For example, in a simple linear pneumatic actuator, compressed air is introduced into one side of the cylinder, pushing the piston outwards. When the air supply is cut off and the air is exhausted, a spring inside the cylinder pulls the piston back to its starting position.
Types of Pneumatic Actuators
Double - Acting Pneumatic Actuators
- In double - acting pneumatic actuators, compressed air is used to both extend and retract the piston. This provides greater force and speed compared to single - acting actuators. In airport runway lighting systems, double - acting pneumatic actuators are used to control the raising and lowering of lights. When the runway needs to be illuminated, compressed air is supplied to extend the lights, and when they need to be retracted (such as during maintenance or when not in use), air is supplied to the other side of the piston to pull the lights back down.
- These types of actuators are also commonly used in aircraft cargo door systems. The double - acting mechanism ensures that the cargo doors can be opened and closed with sufficient force, even in challenging environmental conditions.
Single - Acting Pneumatic Actuators
- Single - acting pneumatic actuators use compressed air to move the piston in one direction, and a spring is used to return it to its original position. These types of actuators are often used in applications where a simpler and more cost - effective solution is required. In some smaller airport facilities, single - acting pneumatic actuators may be used to control the opening and closing of small access doors or hatches. For example, in a utility room in an airport, a single - acting pneumatic actuator can be used to open a door that provides access to electrical or plumbing systems.
Benefits for Airport Equipment
- High - Speed Operation: Pneumatic actuators can operate at high speeds, making them suitable for applications where rapid movement is required. In airport security screening systems, pneumatic actuators are used to quickly move conveyor belts and inspection trays, ensuring that passengers and their luggage can be processed efficiently.
- Reliability: These types of actuators are known for their reliability, especially in harsh environments. Compressed air systems are less affected by electrical interference, making pneumatic actuators a good choice for outdoor or industrial - like settings in airports, such as on the tarmac or in aircraft maintenance areas.
- Cost - Effective: Pneumatic actuators are often more cost - effective compared to some other types of actuators, especially in large - scale applications. The initial investment in a pneumatic system, including the compressor and actuators, can be relatively low, and the maintenance costs are also manageable.
Hydraulic Actuators: Delivering High - Force Performance
Hydraulic actuators are designed to generate high levels of force, making them ideal for heavy - duty applications in airport equipment. These types of actuators use hydraulic fluid (usually oil) to transmit power and create mechanical motion.
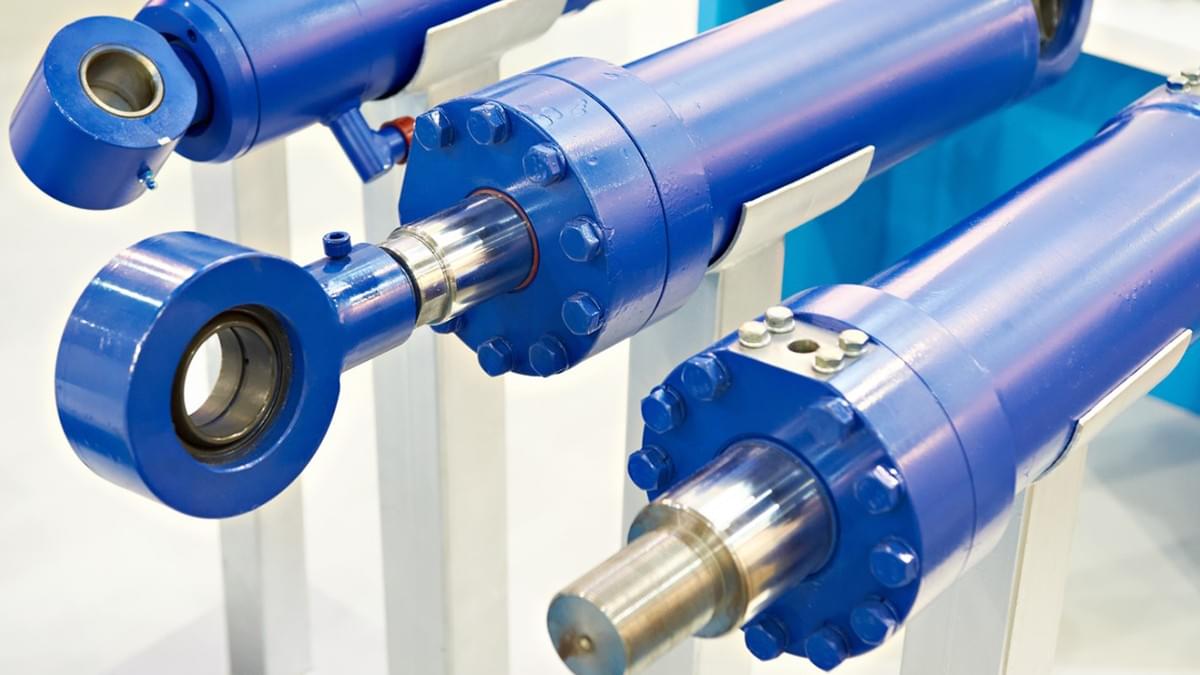
Operation Mechanism
Hydraulic actuators work on the principle of Pascal's law, which states that pressure applied to an enclosed fluid is transmitted undiminished to every portion of the fluid and the walls of the containing vessel. A hydraulic pump is used to pressurize the hydraulic fluid. This pressurized fluid is then directed to the actuator, which contains a cylinder and a piston. The pressure of the fluid on the piston generates a large amount of force, resulting in linear or rotary motion. For example, in a large hydraulic linear actuator used in aircraft landing gear systems, the pressurized hydraulic fluid pushes the piston, extending or retracting the landing gear. The high force generated by the hydraulic actuator ensures that the landing gear can support the weight of the aircraft during takeoff, landing, and taxiing.
Common Applications in Airports
Aircraft Ground Support Equipment
- Hydraulic actuators are widely used in aircraft ground support equipment. In aircraft tow tractors, these types of actuators are used to control the steering and lifting mechanisms. The high - force output of hydraulic actuators allows the tow tractor to maneuver large aircraft easily, even in tight spaces on the tarmac. Additionally, in aircraft cargo loaders, hydraulic actuators are used to lift and position heavy cargo containers onto the aircraft. The precise control of the hydraulic actuator ensures that the cargo is loaded safely and accurately.
Runway Maintenance Equipment
- In runway maintenance, hydraulic actuators play a crucial role. Runway sweepers and snowplows used in airports are often equipped with hydraulic actuators. The high - force capabilities of these types of actuators enable the sweepers to clean the runway effectively, removing debris and dirt. In snowy conditions, snowplows with hydraulic actuators can clear the runway quickly, ensuring that aircraft operations can resume as soon as possible. The hydraulic system also allows for precise control of the plow's position and angle, optimizing the snow - clearing process.
Advantages in Airport Operations
- High Force Output: As mentioned, hydraulic actuators can generate extremely high levels of force. This makes them indispensable for applications where heavy loads need to be moved or lifted, such as in aircraft - related equipment and large - scale runway maintenance machinery.
- Smooth and Precise Operation: Despite their high - force capabilities, hydraulic actuators can provide smooth and precise movement. The flow of hydraulic fluid can be carefully controlled, allowing for accurate positioning of components. This is important in applications where precision is required, even when dealing with heavy loads.
- Durability: Hydraulic systems are generally very durable and can withstand harsh operating conditions. The use of high - quality hydraulic fluids and components ensures that the actuators can operate reliably for long periods, reducing the need for frequent maintenance and replacement.
Selecting the Right Actuator for Airport Equipment
When it comes to choosing the appropriate actuator for airport equipment, several factors need to be considered.
Load Requirements
The first and foremost factor is the load that the actuator needs to handle. Different types of actuators have varying load - carrying capacities. For example, if you are looking for an actuator to operate a small access door in an airport building, a lightweight electric or pneumatic actuator may be sufficient. However, for heavy - duty applications such as moving aircraft or large runway maintenance equipment, hydraulic actuators are the preferred choice due to their high - force output.
Speed and Precision Requirements
The required speed and precision of the operation also play a significant role. If rapid movement is essential, such as in passenger screening systems or runway lighting control, pneumatic actuators may be a good option due to their high - speed capabilities. On the other hand, if precision is of utmost importance, for instance, in the operation of delicate airport instruments or in baggage handling systems where accurate positioning of luggage is required, electric actuators are often the better choice.
Environmental Conditions
Airport environments can be harsh, with exposure to various weather conditions, dust, and vibrations. Pneumatic actuators are relatively immune to electrical interference and can operate well in outdoor and dusty environments. Hydraulic actuators, while durable, need to be properly maintained to prevent fluid leaks, especially in cold or hot weather conditions. Electric actuators may require additional protection in harsh environments to prevent damage to electrical components.
Cost Considerations
Cost is always a factor in any procurement decision. Initial purchase costs, installation costs, and long - term maintenance costs all need to be evaluated. Pneumatic actuators are often more cost - effective in terms of initial investment and maintenance, especially for large - scale applications. Electric actuators may have a higher initial cost but can offer savings in energy consumption over time. Hydraulic actuators, due to their complex systems and the need for high - quality hydraulic fluids, can have relatively high maintenance costs.
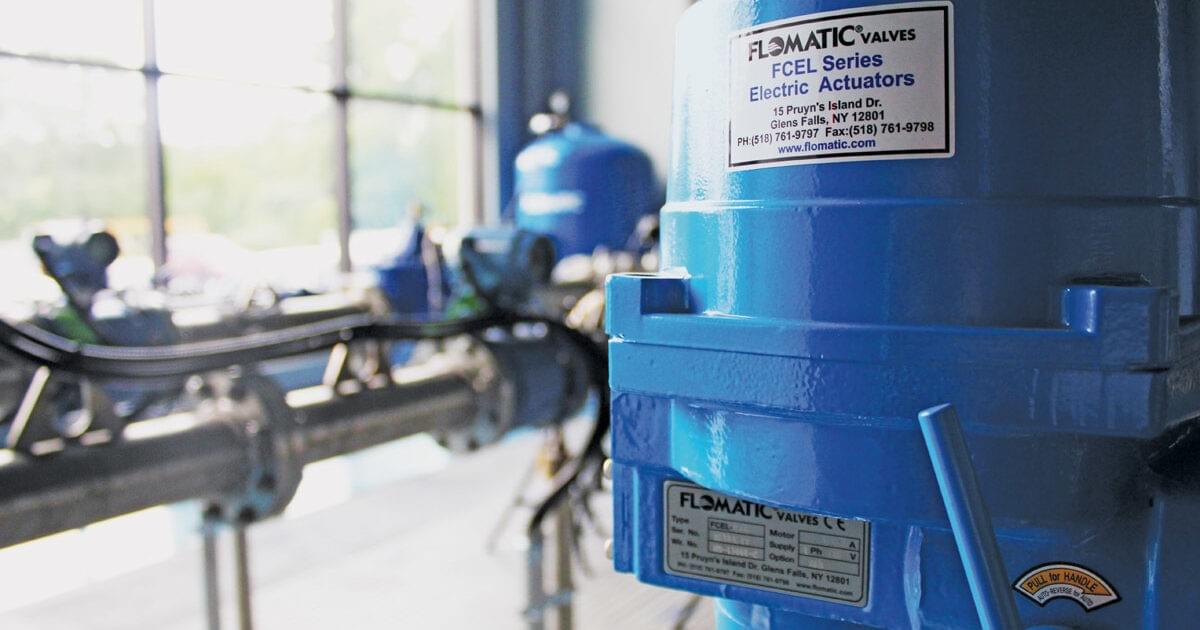
Haisen Global: Your Partner for High - Quality Actuators
At Haisen Global, we understand the unique requirements of airport operations and offer a wide range of high - quality types of actuators. Our electric actuators are designed with the latest technology, providing precise control, energy efficiency, and easy integration with existing airport systems. Our pneumatic actuators are reliable, high - speed, and built to withstand the rigors of airport environments. And our hydraulic actuators are engineered for high - force performance, durability, and smooth operation.
We are committed to providing excellent customer service, from helping you select the right actuator for your specific needs to offering after - sales support and maintenance services. With our extensive experience in the industry and a global network of satisfied customers, we are your trusted partner for all your actuator requirements in airport equipment.
In conclusion, the types of actuators available offer a diverse range of solutions for airport equipment. By understanding the features, applications, and selection criteria of each type, airport operators can make informed decisions to optimize their infrastructure and ensure the smooth and efficient operation of their facilities. Whether it's the precision of electric actuators, the speed of pneumatic actuators, or the high - force performance of hydraulic actuators, there is an actuator type to meet every need in the dynamic world of airport operations.
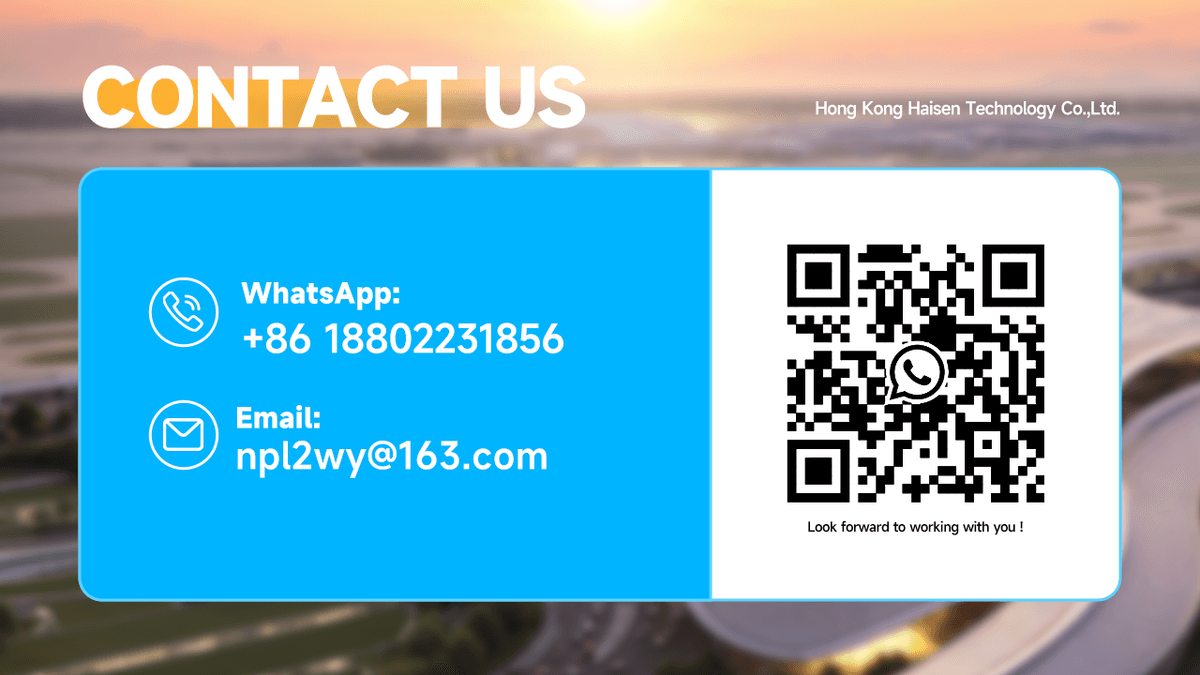