Introduction: Decoding Airplane Fuel Cost Dynamics
In the aviation industry, the question of "airplane fuel cost" lies at the core of operational profitability and strategic planning. Whether for commercial airlines or private operators, understanding how fuel expenses fluctuate and impact flight economics is essential for navigating global markets. This blog delves into the technical nuances of airplane fuel cost, exploring factors from fuel types and aircraft efficiency to refueling technologies and market trends, providing actionable insights for industry professionals and international clients.
The Immense Scale of Fuel Expenditure
- Dominant OPEX: Fuel consistently constitutes 25-40% of an airline's total operating costs (OPEX), dwarfing other expenses like labor and maintenance.
- Price Volatility Impact: Fluctuations in crude oil prices directly translate into significant swings in airline profitability, sometimes determining quarterly profits or losses.
- Operational Sensitivity: Even minor inefficiencies in fuel management cascade into substantial annual costs for large fleets.
The Fundamentals of Airplane Fuel Cost: Market Drivers and Core Variables
Airplane fuel cost is not a static figure but a dynamic metric shaped by global oil markets, geopolitical events, and regional supply-demand dynamics. Crude oil prices, which account for over 70% of jet fuel expenses, fluctuate daily due to OPEC policies, international conflicts, and economic cycles. For instance, a 10% increase in Brent crude oil prices can raise airplane fuel cost for a Boeing 747 by $5,000 per flight, highlighting the urgency of monitoring market trends.
Jet Fuel Types: Jet A vs. Jet A-1 and Pricing Disparities
- Jet A: Primarily used in the U.S., this kerosene-based fuel has a freezing point of -40°C, suitable for domestic flights. Its average price ranges from $2.8 to $3.5 per gallon, varying by region.
- Jet A-1: The international standard, with a lower freezing point (-47°C), ideal for long-haul flights. Pricing typically exceeds Jet A by 5-10% due to higher refining requirements and global distribution costs.
Regional taxes and subsidies further complicate airplane fuel cost. For example, European Union airports impose carbon emission taxes, adding $0.15-$0.30 per gallon to Jet A-1, while some Middle Eastern countries offer subsidized fuel, reducing costs by 20-30%.
Aircraft-Specific Fuel Cost Calculations: From 737 to 747
Boeing 737: Fuel Capacity and Cost Models
The Boeing 737, a workhorse in regional aviation, has a fuel capacity of 6,875 liters (1,820 gallons). At an average jet fuel price of $3 per gallon, filling a 737 costs approximately $5,460. However, real-world costs fluctuate based on:
- Route altitude: Flights above 35,000 feet require Jet A-1, increasing costs by $500-$1,000 versus domestic Jet A refuels.
- Payload weight: Each additional 1,000 kg of cargo raises fuel consumption by 3-5%, adding $150-$250 to total airplane fuel cost.
Boeing 747: The Jumbo Jet’s Fuel Expenditure
The iconic 747 boasts a massive fuel capacity of 26,000 liters (6,900 gallons), translating to a refueling cost of $20,700 at $3 per gallon. Long-haul operations further inflate costs:
- A 10-hour transatlantic flight consumes 80% of the 747’s fuel capacity, costing $16,500-$18,000.
- Seasonal demand spikes (e.g., summer holidays) can raise fuel prices by 15-20%, pushing 747 refuel costs to $24,000.
Technical Innovations in Refueling: Reducing Airplane Fuel Cost
Haisen’s Aircraft Pipeline Refueling Truck: Efficiency Redefined
Haisen’s advanced refueling trucks feature:
- High-flow piping systems: Capable of dispensing 1,200 liters per minute, reducing refuel time for a 737 from 25 to 12 minutes.
- Integrated filtration technology: Removes 99.9% of particulate matter and moisture, preventing engine corrosion and improving fuel efficiency by 2-3%.
- Pneumatic control systems: Enables precise fuel volume adjustment, minimizing overfill waste (typically 0.5-1% of total fuel cost).
For operators, this technology translates to tangible savings: a 747 refueling with Haisen’s truck saves $300-$500 per session due to reduced labor costs and fuel waste.
Low-Altitude Hydrant Dispensers: Optimizing Underwing Refueling
These 2-meter-tall dispensers offer:
- Maneuverability: Compatible with narrow-body and wide-body aircraft, reducing ground crew setup time by 40%.
- Flow rate precision: Adjustable from 500 to 1,500 liters per minute, matching aircraft fuel system requirements.
- Weather resistance: Sealed hydraulic systems operate in -30°C to +50°C environments, ensuring consistent performance in global climates.
Airlines using low-altitude hydrants report a 15% reduction in annual airplane fuel cost due to minimized tarmac delays and optimized refueling cycles.
Long-Haul Flight Economics: Calculating 10-Hour Journey Costs
Fuel Burn Rates and Cost Projections
A 10-hour flight on a Boeing 787 consumes ~18,000 gallons of Jet A-1, costing $54,000 at $3 per gallon. Key variables include:
- Cruise speed: Mach 0.85 vs. Mach 0.80 increases fuel burn by 8%, adding $4,300 to costs.
- Wind patterns: Tailwinds can reduce fuel consumption by 10%, while headwinds raise it by 15%.
Fuel Hedging Strategies for Cost Stability
Airlines often use financial hedging to mitigate price volatility:
- Swaps and futures contracts: Lock in fuel prices for 6-12 months, reducing uncertainty. For example, a carrier hedging at $2.9 per gallon saves $1,200 per 737 refuel if market prices rise to $3.3.
- Collars: Sets a price floor and ceiling, balancing risk. A collar between $2.7 and $3.2 protects against spikes while allowing gains from price drops.
Environmental Factors and Future Fuel Cost Trends
Sustainable Aviation Fuels (SAFs): Cost vs. Compliance
SAFs, derived from waste oils or plant matter, currently cost 30-50% more than traditional jet fuel. However:
- Government incentives: EU’s Emissions Trading System (ETS) offers carbon credits for SAF use, offsetting 15-20% of higher costs.
- Technological advancements: Second-generation SAFs (from agricultural waste) aim to reduce production costs by 40% by 2030.
Regulatory Impacts on Airplane Fuel Cost
- ICAO CORSIA: Requires airlines to offset carbon emissions for international flights, increasing operational costs by 2-3%.
- Regional bans: Norway’s 2030 jet fuel tax hike could raise costs by $0.50 per gallon, impacting trans-Arctic routes.
Operational Strategies to Minimize Airplane Fuel Cost
Route Optimization and Fuel Efficiency
- Continuous Descent Operations (CDO): Reduces fuel burn by 3-5% on landing approaches.
- Reduced Vertical Separation Minimums (RVSM): Enables more efficient cruising altitudes, saving 1-2% fuel per flight.
Fleet Modernization: New-Generation Aircraft
- Boeing 737 MAX: 14% more fuel-efficient than previous 737 models, saving $2,000 per 10-hour flight.
- Airbus A350: Composite materials and efficient engines cut fuel costs by 25% versus older wide-body jets.
Mastering the Complex Equation
Airplane fuel cost is a dynamic and multifaceted challenge, far exceeding the simple price per gallon at the pump. It encompasses global oil markets, complex refining, intricate logistics, diverse local fees, evolving environmental regulations, and the intrinsic efficiency of aircraft and operations. For airlines, relentless focus on optimizing every factor within their control – fleet choice, flight operations, weight management, and precise fuel procurement – is essential for survival and competitiveness. For foreign clients involved in supplying aviation infrastructure and equipment, understanding this complex cost structure is vital. Providing solutions that enhance airplane fuel cost efficiency – particularly through highly accurate, reliable, and efficient fueling systems, filtration technology, and fuel management software – represents a significant value proposition. Investing in modern equipment isn't just an operational upgrade; it's a strategic move directly contributing to an airline's bottom line by mitigating its single largest expense. As environmental pressures mount and fuel price volatility persists, the demand for technologies that deliver tangible reductions in airplane fuel cost and emissions will only intensify. Mastering this complex equation is the key to sustainable aviation operations and a compelling business opportunity for innovative equipment providers.
Conclusion: Navigating Airplane Fuel Cost in a Dynamic Landscape
Airplane fuel cost remains a critical metric for aviation stakeholders, influenced by technical, market, and regulatory factors. From choosing between Jet A and Jet A-1 to implementing advanced refueling technologies like Haisen’s pipeline trucks, every decision impacts the bottom line. As the industry evolves toward sustainability, integrating SAFs and hedging strategies will become essential for managing costs while meeting environmental goals. For international clients, partnering with innovative equipment providers and adopting data-driven fuel management systems is key to optimizing operations in an ever-changing market.
By prioritizing efficiency, leveraging technology, and staying abreast of global trends, airlines and operators can transform airplane fuel cost from a challenge into a competitive advantage. Contact Haisen Global today to explore how our refueling solutions can enhance your fuel management strategy and drive long-term profitability.
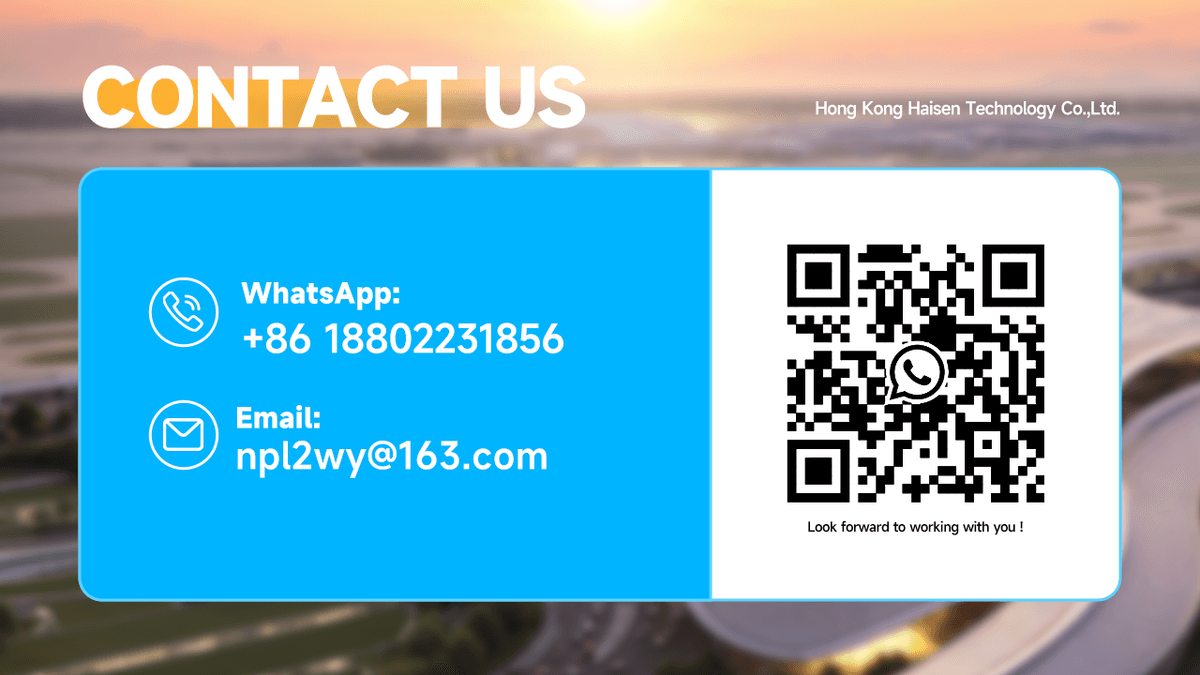