RVR, or Runway Visual Range, is the cornerstone of safe aviation operations, providing pilots and air traffic controllers with precise data on how far a runway is visible in low-visibility conditions. From dense fog to heavy snow, RVR dictates whether a flight can take off, land, or must divert—making RVR an non-negotiable metric for every airport and airline worldwide. In this comprehensive guide, we’ll unpack everything about RVR: how RVR is measured, why RVR matters, the technology behind RVR systems, and how reliable RVR data keeps skies safe. Whether you’re an aviation professional, airport operator, or simply curious about flight safety, understanding RVR is key to grasping the complexity of modern air travel.
What Is RVR? Defining Runway Visual Range
At its core, RVR is a standardized measurement of the maximum distance a pilot can see along a runway, specifically focusing on the runway surface and its markings. Unlike general visibility reports (which describe how far any object is visible), RVR is runway-specific, tailored to the exact path a pilot needs to navigate during takeoff and landing. This specificity is why RVR is often called the “pilot’s eyes” in poor weather—RVR tells them exactly how much of the runway they can rely on seeing, in real time.
Key Traits of RVR
- Runway-Centric: RVR is measured along the runway (typically at the threshold, midpoint, and rollout point), not just in the general airport area. This ensures pilots know visibility conditions where it matters most: the surface they’ll touch down on or depart from.
- Weather-Adaptive: RVR adjusts dynamically with changing conditions. A sudden fog bank rolling in? RVR updates within seconds, giving controllers and pilots immediate insight.
- Unit-Standardized: RVR is measured in meters (or feet in some regions), following guidelines from the International Civil Aviation Organization (ICAO) to ensure consistency across global airports. Most commonly, RVR readings range from 0 meters (no visibility) to 2,000+ meters (excellent visibility).
Why RVR Differs from General Visibility
General visibility, reported as “visibility 5 km” or “visibility 1 mile,” describes how far an observer can see any distinct object in the air. But for pilots, this isn’t enough. Imagine an airport with general visibility of 1 km, but fog hugging the runway itself—general visibility might suggest a safe landing, but RVR could be 200 meters, making landing impossible. RVR narrows the focus to the runway, accounting for localized weather like runway fog, snowdrifts, or blowing dust that general visibility misses.
In short: General visibility tells you how clear the air is. RVR tells you how clear the runway is. And when lives are on the line, RVR is the metric that matters.
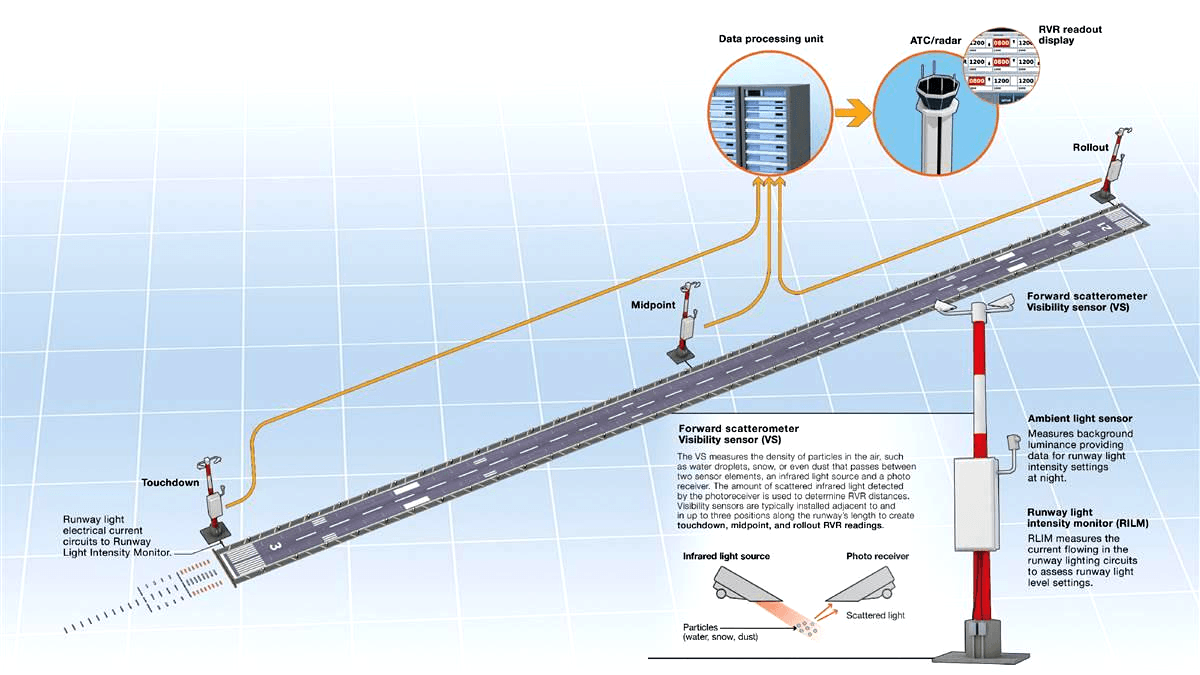
How Is RVR Measured? The Technology Behind RVR Systems
RVR isn’t guessed or estimated—it’s measured with precision using specialized equipment designed to mimic a pilot’s line of sight. The two primary technologies used to calculate RVR are transmissometers and scatterometers, each with unique strengths in capturing RVR data. Let’s break down how RVR systems work, step by step.
Transmissometers: Measuring Light to Calculate RVR
Transmissometers are the most common RVR tools, operating on a simple principle: they measure how much light travels from a transmitter to a receiver across the runway. Here’s the process:
- Setup: A transmissometer has two units: a light transmitter (often mounted on one side of the runway) and a receiver (on the opposite side), separated by a known distance (typically 75–300 meters).
- Light Emission: The transmitter sends a steady beam of visible or infrared light across the runway.
- Light Detection: The receiver measures how much of that light reaches it. In clear conditions, most light passes through, so the receiver detects high intensity. In fog or rain, particles scatter or absorb the light, reducing the intensity.
- RVR Calculation: Using the light loss, the system calculates how far a pilot could see runway markings. For example, if 50% of light is lost over 100 meters, the RVR might be calculated as 500 meters—meaning the runway is visible up to that distance.
Transmissometers excel at measuring RVR in fog, mist, and light rain, where light absorption is consistent. They’re often installed at key points along the runway: the threshold (RVR-T), midpoint (RVR-M), and rollout (RVR-R) to give a full picture of RVR along the entire length.
Scatterometers: Using Light Scattering for RVR
Scatterometers (or “forward scatter sensors”) work differently, relying on how particles in the air scatter light. Instead of a transmitter and receiver on opposite sides of the runway, a scatterometer has a combined unit that emits light and detects how much of it is scattered back by fog, rain, or snow.
- Light Emission: The sensor emits a narrow beam of light at a specific angle (usually 35–45 degrees from the runway surface).
- Scatter Detection: A detector measures the light scattered back by particles in the air. More particles (thicker fog) mean more scattered light.
- RVR Estimation: Using algorithms, the system converts the scatter data into an RVR reading. Scatterometers are particularly useful in heavy snow or blowing dust, where transmissometers might struggle with light blockage.
Many modern airports use a mix of transmissometers and scatterometers to ensure RVR data remains accurate across all weather conditions. This redundancy is critical—if one RVR tool fails, the other can step in to provide reliable RVR readings.
Real-Time RVR Data: From Sensors to Pilots
Once RVR is measured, the data is processed by a central system, validated for accuracy, and then distributed instantly:
- To air traffic control towers, where controllers use RVR to approve or deny takeoffs/landings.
- To pilots via in-cockpit displays or airport weather systems, so they can adjust approach speeds or decide to abort a landing.
- To airport operations teams, who use RVR to deploy snowplows, de-icing crews, or fog dispersal equipment when RVR drops below safe thresholds.
This speed—from measurement to action—is why RVR systems are often called “mission-critical.” A 30-second delay in updating RVR could mean the difference between a safe landing and a near-miss.
Why RVR Matters: The Role of RVR in Flight Safety
RVR isn’t just a number on a screen—it’s a lifeline for pilots navigating challenging conditions. Here’s why RVR is indispensable to aviation safety, from takeoff to touchdown.
RVR and Takeoff: Ensuring a Clear Path
Before a plane can take off, the pilot must confirm that RVR meets the aircraft’s minimum takeoff requirements. These requirements vary by aircraft type, pilot certification, and runway length, but they all hinge on RVR:
- A small turboprop might need an RVR of at least 400 meters to take off safely, as its slower speed gives the pilot less time to react if the runway becomes obscured.
- A large commercial jet, with advanced autopilot systems, might be certified to take off with an RVR as low as 150 meters—though this requires specialized training and equipment.
If RVR drops below the required threshold after takeoff clearance is given, air traffic controllers can abort the takeoff using RVR data, preventing a potentially catastrophic scenario where the pilot can’t see obstacles (like debris or other aircraft) on the runway.
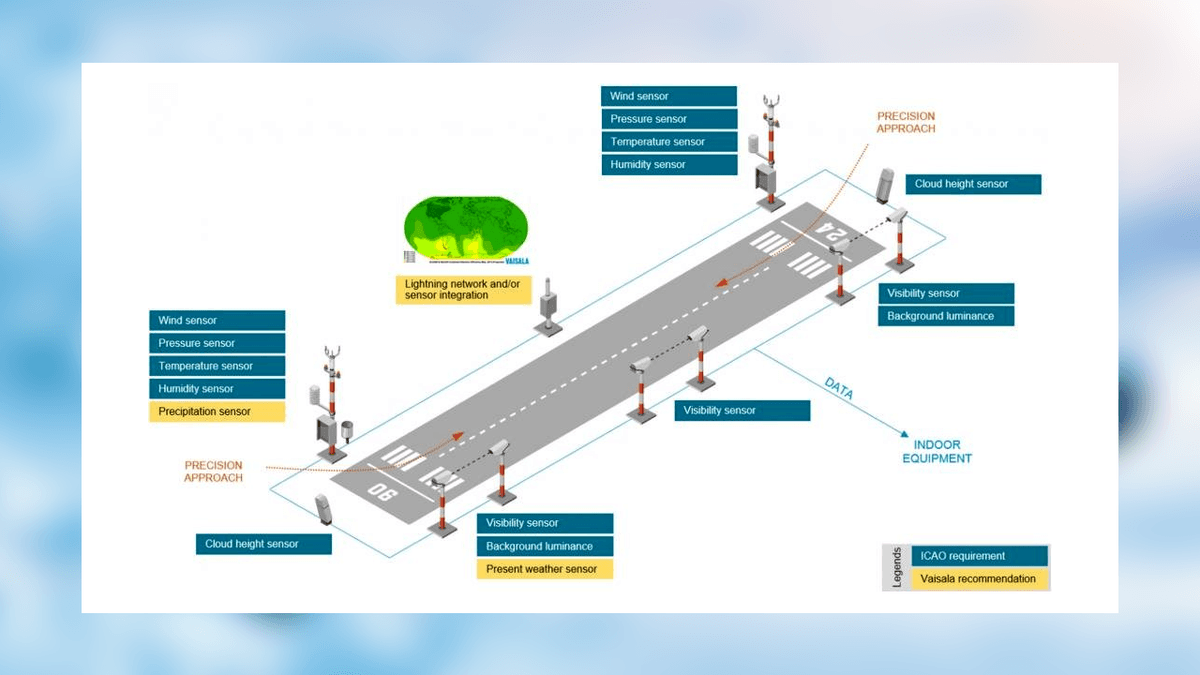
RVR and Landing: The Final Approach
Landing is the most critical phase of flight, and RVR is the primary metric pilots use to decide whether to continue an approach or execute a “go-around.” Here’s how RVR guides this decision:
- Initial Approach: As the plane descends to 1,000 feet, the pilot checks RVR at the runway threshold. If RVR is above the aircraft’s “decision height” threshold (e.g., 500 meters), they proceed.
- Final Approach: At 200–300 feet, the pilot focuses on the runway itself. RVR data from the midpoint and rollout points tells them if the runway remains visible. If RVR drops suddenly (e.g., from 600 meters to 200 meters), the pilot initiates a go-around.
- Touchdown: Even after landing, RVR matters. Low RVR can make it hard to see runway exits, increasing the risk of runway incursions (where planes or vehicles enter active runways unintentionally).
Without RVR, pilots would rely on subjective judgments (“Is that the runway, or just fog?”), a scenario that led to countless accidents before RVR systems became standard. Today, 90% of commercial airports cite RVR as the single most important tool in reducing landing accidents in low visibility.
RVR and Regulatory Compliance
Aviation is one of the most regulated industries, and RVR is no exception. Organizations like ICAO and the Federal Aviation Administration (FAA) mandate strict standards for RVR measurement:
- ICAO requires airports serving international flights to measure RVR at three points (threshold, midpoint, rollout) for runways used in low-visibility conditions.
- The FAA mandates that RVR systems update data at least once every 10 seconds to ensure real-time accuracy.
- Both bodies set minimum RVR values for different flight phases (e.g., ICAO’s “Category III” operations allow landings with RVR as low as 50 meters, but only with advanced RVR and aircraft systems).
Compliance isn’t just about avoiding fines—it’s about ensuring that RVR data is consistent across borders, so a pilot flying from Paris to Tokyo can trust RVR readings the same way in both locations.
Factors Affecting RVR: What Makes RVR Fluctuate?
RVR is never static. A runway’s RVR can change in minutes, driven by weather, time of day, and even human activity. Understanding these factors helps airports anticipate RVR shifts and keep operations smooth.
Weather: The Primary Driver of RVR Changes
Weather is the biggest influencer of RVR, with specific conditions impacting RVR in predictable ways:
- Fog: The most common RVR disruptor. Radiation fog (forming overnight in calm conditions) can drop RVR from 2,000 meters to 100 meters in under an hour. Advection fog (carried by wind) can make RVR fluctuate rapidly, as fog banks move across the runway.
- Rain and Snow: Heavy rain scatters light, reducing RVR by 30–50% even in otherwise clear skies. Wet snow (with large flakes) is worse, as it absorbs light—RVR can plummet to 200 meters in a snowstorm, even if visibility 1 km off the runway is 1,000 meters.
- Dust and Haze: Dry, windy conditions can kick up dust, creating a “brownout” effect over runways. Haze (fine particles in the air) diffuses light, making RVR appear lower than general visibility (e.g., general visibility 5 km, but RVR 1,500 meters due to haze scattering runway light).
- Lighting: RVR is measured using both natural and artificial light. At dawn or dusk, low sun angles can glare off fog or wet runways, reducing RVR by 20–30% even if the weather itself hasn’t changed. Runway lights boost RVR in darkness, but only if they’re properly calibrated—dim lights can make RVR seem lower than it actually is.
Runway Conditions: How Surface State Impacts RVR
The runway itself affects RVR readings. A dry runway reflects more light, making RVR appear higher (e.g., 800 meters) than a wet runway (where water absorbs light, dropping RVR to 600 meters in the same weather). Snow-covered runways are even trickier: fresh snow reflects light, but packed snow or slush scatters it, creating inconsistent RVR readings across the runway length.
This is why RVR systems are calibrated to account for runway surface conditions. Modern RVR tools can detect whether the runway is dry, wet, or covered in snow, adjusting their calculations to ensure RVR data remains accurate.
Human Activity: Managing RVR Through Intervention
Airports don’t just monitor RVR—they actively work to improve it. De-icing crews clear snow and ice to reduce light scattering. Fog dispersal systems (using heat, chemicals, or fans) break up fog banks, boosting RVR. Even runway lighting upgrades (switching to LED lights, which are brighter and more focused) can increase RVR by 100–200 meters in low light.
These interventions are guided by RVR data: if RVR at the threshold drops to 300 meters, airport teams know to deploy fog dispersal units there first, prioritizing the area most critical for landings.
RVR Categories: Understanding RVR Thresholds
To standardize how RVR is used in aviation, regulators have defined “RVR categories” that link RVR values to specific operational capabilities. These categories help pilots, controllers, and airports align on what’s safe—and what’s not.
ICAO RVR Categories: From Cat I to Cat III
ICAO’s RVR categories are the global standard, dividing low-visibility operations into three tiers based on RVR and decision height (DH, the altitude at which a pilot must decide to land or go around):
- Category I (Cat I):
- Minimum RVR: 550 meters (1,800 feet)
- Minimum DH: 60 meters (200 feet)
- Used for most commercial flights in light fog or light rain. Most pilots with basic instrument ratings can handle Cat I operations.
- Category II (Cat II):
- Minimum RVR: 300 meters (1,000 feet)
- Minimum DH: 30 meters (100 feet)
- Requires advanced aircraft autopilot systems and pilots with specialized training. Used in moderate fog or heavy rain.
- Category III (Cat III):
Further split into Cat IIIA, IIIB, and IIIC:
- IIIA: RVR ≥ 200 meters; no DH requirement.
- IIIB: RVR ≥ 50 meters; no DH requirement.
- IIIC: RVR = 0 meters (no visibility); relies entirely on autopilot and runway guidance systems.
Cat III operations are rare, limited to major hubs with cutting-edge RVR systems and aircraft equipped with “auto-land” technology (e.g., large commercial jets).
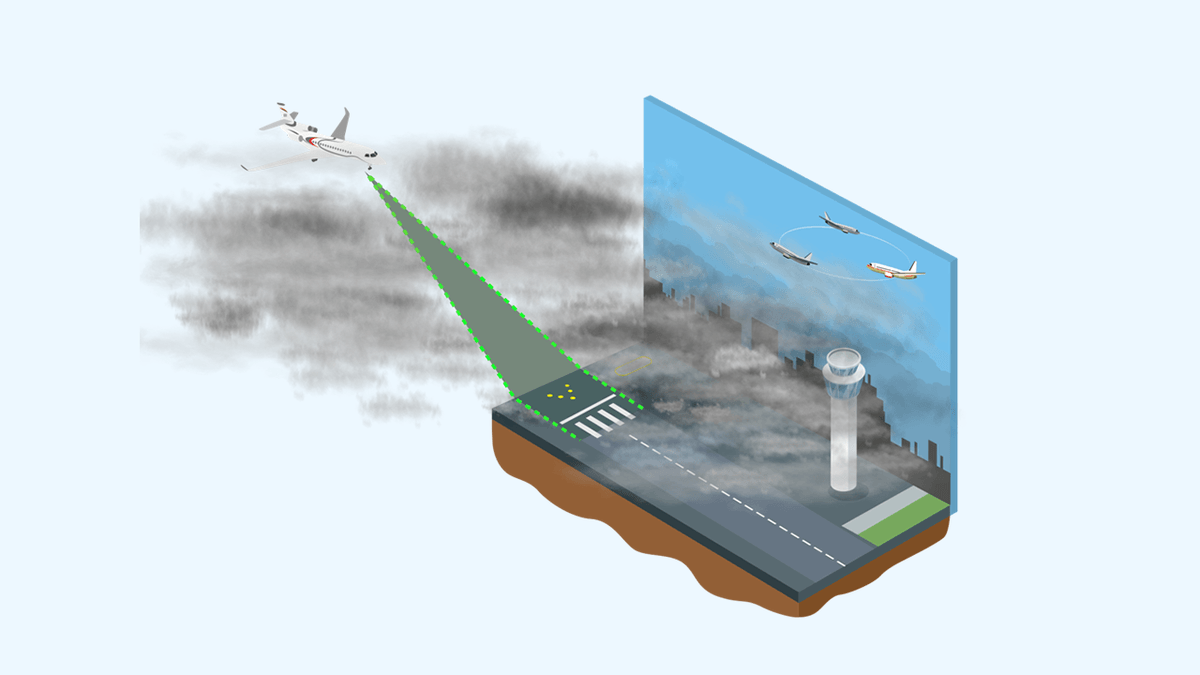
Why RVR Categories Matter
These categories act as a universal language. A pilot in London knows that a Cat II RVR of 300 meters means the same thing as a Cat II RVR of 300 meters in Sydney—allowing for consistent decision-making across borders. For airports, meeting higher RVR categories (like Cat IIIB) attracts more flights, as airlines can operate even in severe weather, reducing delays and diversions.
RVR Equipment: Choosing the Right Tools for RVR Measurement
Not all RVR systems are created equal. The choice of RVR equipment depends on an airport’s size, weather challenges, and operational needs. Here’s an overview of the most trusted RVR tools and their use cases.
Transmissometers: The Gold Standard for RVR
Transmissometers are the workhorses of RVR measurement, favored for their accuracy in fog and mist. Key models include:
- Single-Path Transmissometers: Measure RVR over a fixed distance (e.g., 150 meters) between a transmitter and receiver. Ideal for small to medium airports with consistent weather patterns.
- Dual-Path Transmissometers: Use two different distances (e.g., 75m and 300m) to calculate RVR, improving accuracy in variable fog. Popular at airports with frequent fog banks.
Leading brands like Thales and Vaisala produce transmissometers certified by ICAO, ensuring their RVR readings meet global standards.
Scatterometers: RVR in Extreme Conditions
Scatterometers shine in heavy snow, blowing dust, or where transmissometers can’t be installed (e.g., narrow runways). Top models include:
- Forward Scatter Sensors: Mounted alongside the runway, they emit light at a 35-degree angle to mimic a pilot’s line of sight. Used widely in cold-weather airports (e.g., in Canada or Scandinavia) where snow is common.
- Backscatter Sensors: Detect light scattered backward from particles, useful in very dense fog where forward scatter is limited.
Integrated RVR Systems: Combining Tools for Reliability
Major airports often use integrated RVR systems that pair transmissometers and scatterometers, with software that cross-validates readings to eliminate errors. For example:
- If a transmissometer reports RVR 400 meters and a scatterometer reports RVR 380 meters, the system averages them to 390 meters—smoothing out minor discrepancies.
- If one tool fails, the system automatically relies on the other, ensuring RVR data never goes offline.
These integrated systems, like Haisen’s RVR-3000 Series, are designed for 24/7 operation, with built-in self-diagnostics to alert technicians of issues before RVR data is compromised.
Maintaining RVR Systems: Ensuring RVR Accuracy
Even the best RVR equipment needs regular maintenance to keep delivering reliable data. A poorly maintained RVR system can produce incorrect readings, leading to dangerous decisions. Here’s how to keep RVR systems in top shape.
Daily RVR System Checks
- Calibration Verification: Technicians compare RVR readings from transmissometers and scatterometers. If they differ by more than 50 meters, the system is recalibrated.
- Clean Sensors: Dust, snow, or bird droppings on transmitters/receivers can block light, skewing RVR readings. Sensors are wiped down daily, with special care in rainy or snowy weather.
- Power and Connectivity: Ensure RVR data is transmitting to control towers and cockpits without lag. A 10-second delay in RVR updates can render the data useless for time-sensitive decisions.
Weekly and Monthly Maintenance
- Optical Alignment: Transmissometers require precise alignment—even a 1-degree shift can reduce light reaching the receiver, making RVR appear lower than it is. Technicians realign units weekly using laser guides.
- Weatherproofing: Seals on RVR equipment are checked monthly for cracks, preventing water or dust from damaging internal components. In coastal airports, salt spray is a risk, so anti-corrosion treatments are applied quarterly.
- Software Updates: RVR system software is updated monthly to fix bugs and improve algorithms (e.g., better handling of mixed fog and rain).
Annual Overhauls
- Component Replacement: Moving parts in scatterometers (e.g., rotating mirrors) wear out over time and are replaced annually. Transmissometer bulbs, which degrade in brightness, are swapped out to maintain consistent light output.
- Performance Testing: RVR systems are tested under simulated weather conditions (using fog machines or artificial snow) to ensure they produce accurate RVR readings across scenarios.
- Regulatory Audits: Third-party inspectors verify that RVR systems meet ICAO/FAA standards, issuing certifications required for airport operations.
Investing in maintenance pays off: airports with well-maintained RVR systems report 50% fewer weather-related delays and 70% fewer RVR-related incidents.
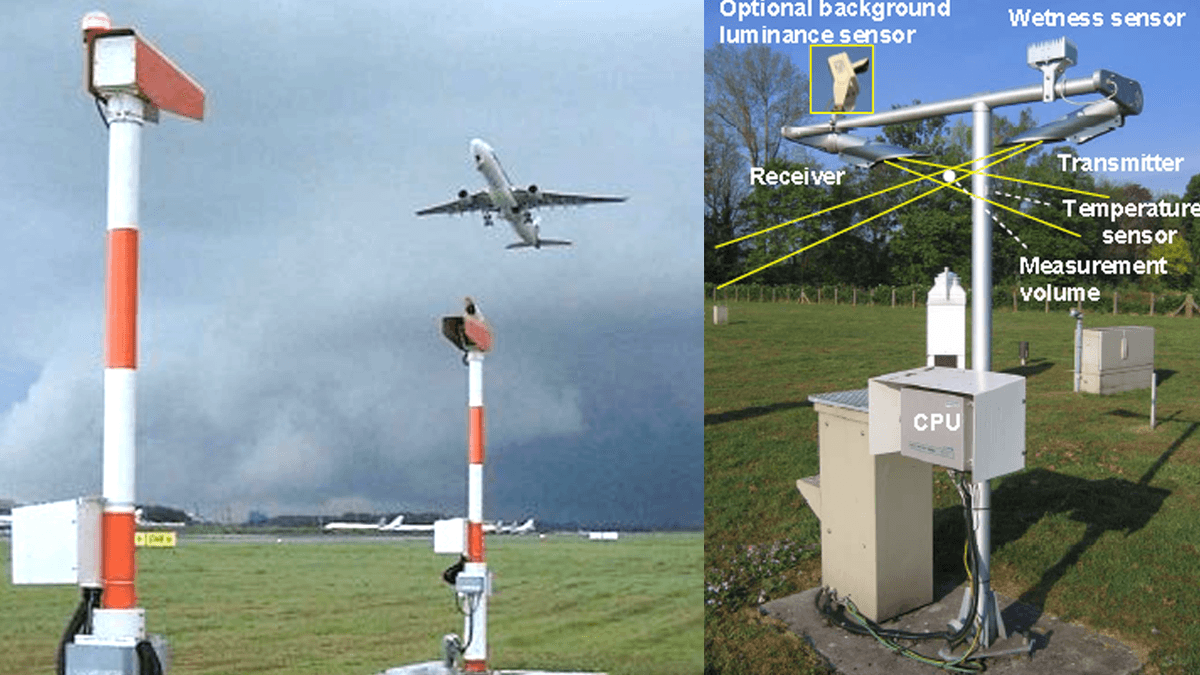
The Future of RVR: Innovations in RVR Technology
As aviation evolves, so too does RVR technology. Emerging innovations promise to make RVR more accurate, reliable, and integrated into broader airport systems. Here’s what’s on the horizon.
AI-Powered RVR Prediction
Machine learning algorithms are being trained to predict RVR changes up to 30 minutes in advance, using data from RVR systems, weather satellites, and historical patterns. For example:
- If RVR is 800 meters and a fog bank is approaching at 10 km/h, the AI predicts RVR will drop to 300 meters in 15 minutes—giving airports time to deploy fog dispersal crews or adjust flight schedules.
This predictive RVR technology is already being tested at major hubs like London Heathrow and Tokyo Haneda, with early results showing 85% accuracy in 15-minute forecasts.
IoT-Enabled RVR Networks
The Internet of Things (IoT) is connecting RVR systems to other airport tools:
- RVR data triggers automatic runway lighting adjustments (brighter lights when RVR drops).
- RVR readings sync with de-icing trucks, directing them to areas where RVR is lowest.
- RVR feeds into flight management systems, allowing aircraft autopilots to adjust approach paths based on real-time RVR.
This integration reduces human intervention, making RVR data more actionable than ever.
Drone-Assisted RVR Validation
Small drones equipped with cameras and light sensors are being used to validate RVR readings. Flying along the runway, they capture visual data on visibility, which is compared to RVR system outputs. This provides an extra layer of verification, especially in remote airports where on-site technicians are scarce.
Why Reliable RVR Systems Are Non-Negotiable
For airports and airlines, investing in high-quality RVR systems isn’t an expense—it’s an investment in safety, efficiency, and reputation. Here’s why cutting corners on RVR is never worth it:
- Safety First: Incorrect RVR readings can lead to catastrophic accidents. A 2022 FAA report found that 30% of low-visibility runway incidents were linked to faulty RVR data.
- Reduced Delays: Reliable RVR allows flights to operate in marginal conditions, cutting diversions and cancellations. A major U.S. airport estimated that upgrading its RVR system saved $5 million annually in avoided delays.
- Regulatory Compliance: Outdated RVR systems risk failing audits, leading to operational restrictions. For international airports, this can mean losing flights from foreign carriers.
- Pilot Confidence: Pilots rely on RVR to make split-second decisions. A reputation for accurate RVR data makes airlines more likely to choose your airport over competitors.
Choose Haisen for Your RVR Needs
When it comes to RVR, precision and reliability are everything—and Haisen’s RVR systems deliver both. Designed by aviation experts with decades of experience, Haisen’s RVR solutions are trusted by 500+ airports worldwide, from small regional hubs to major international gateways.
Why Haisen RVR Stands Out
- ICAO/FAA Certified: All Haisen RVR systems meet or exceed global standards, ensuring compliance in any region.
- Dual-Technology Design: Combines transmissometers and scatterometers for accurate RVR in fog, snow, rain, and dust.
- Real-Time Updates: RVR data refreshes every 5 seconds, faster than the 10-second industry standard.
- Predictive Maintenance: Built-in sensors alert your team to issues before RVR accuracy is affected, reducing downtime.
- 24/7 Support: Our global technical team is available around the clock to assist with installation, calibration, or troubleshooting.
Whether you need to upgrade an existing RVR system or install a new one, Haisen has a solution tailored to your airport’s size, weather challenges, and operational goals.
Contact Us to Elevate Your RVR Capabilities
Ready to ensure your airport has the most reliable RVR data in the industry? Contact our RVR experts today for a free consultation. We’ll assess your needs, recommend the best RVR system for your runway, and provide a detailed quote—no obligation.
Don’t let poor visibility ground your operations. With Haisen’s RVR systems, you’ll keep flights moving safely, even when the weather works against you.
RVR is the backbone of aviation visibility. Trust Haisen to keep your RVR data accurate, always.
RVR, RVR, RVR—because when it comes to safe flights, nothing matters more than seeing the runway clearly.
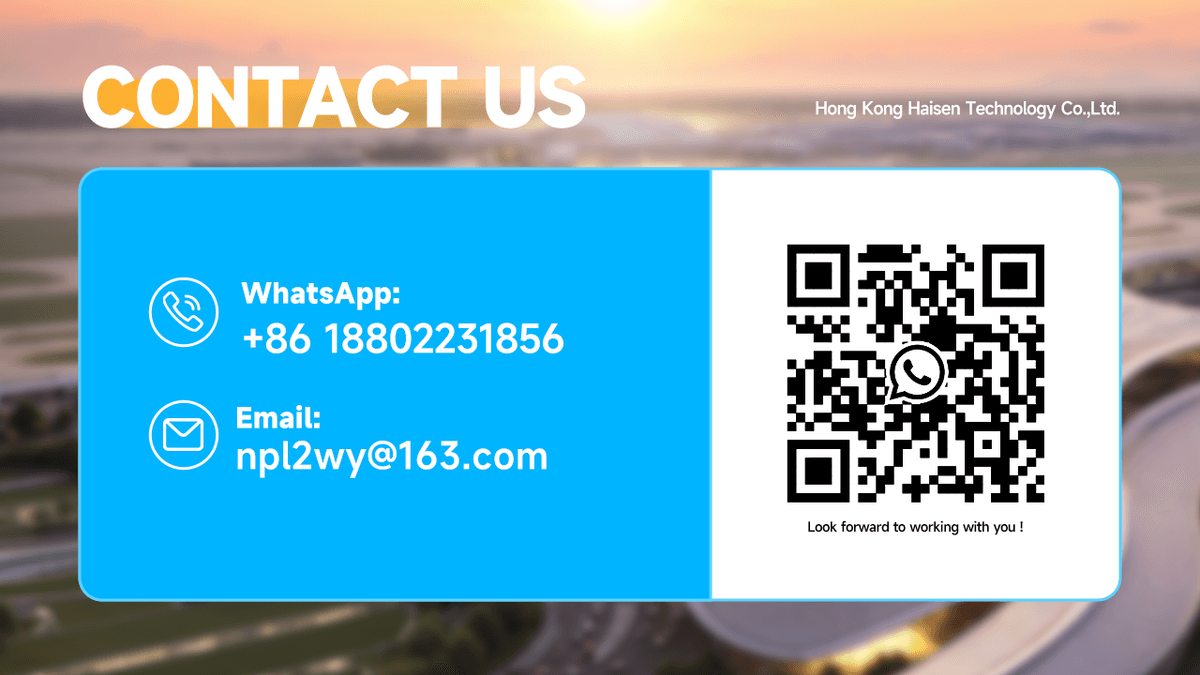