In the intricate world of industrial and commercial systems, electric valve actuators play a pivotal role. These devices are the driving force behind the operation of valves, controlling the flow of fluids such as water, gas, oil, and various chemicals. Whether in a power plant, a water treatment facility, an oil refinery, or a heating and cooling system in a large building, electric valve actuators are essential components for ensuring efficient, safe, and reliable operations.
Understanding Electric Valve Actuators
What is an Electric Valve Actuator?
An electric valve actuator is a device that converts electrical energy into mechanical motion to operate a valve. It receives an electrical control signal, typically from a control system such as a Programmable Logic Controller (PLC) or a Distributed Control System (DCS), and uses this signal to position the valve either fully open, fully closed, or at any intermediate position. This precise control over the valve's position allows for accurate regulation of fluid flow rates, pressures, and temperatures in a wide range of applications.
Types of Electric Valve Actuators
Part - Turn Electric Valve Actuators
- These actuators are designed to rotate a valve stem through a 90 - degree arc, typically used for valves like ball valves, butterfly valves, and plug valves. They are known for their quick operation and high torque output in a relatively compact size. For example, in a natural gas distribution system, part - turn electric valve actuators can rapidly open or close ball valves to control the flow of gas, ensuring safe and efficient distribution.
- The operation of part - turn actuators is often achieved through a motor - driven gear mechanism. The motor rotates the gears, which in turn rotate the valve stem. Some advanced part - turn actuators are equipped with position sensors that can provide feedback to the control system, indicating the exact position of the valve. This feedback is crucial for applications where precise control is required, such as in chemical processing plants where the accurate regulation of fluid flow can affect the quality of the final product.
Multi - Turn Electric Valve Actuators
- Multi - turn actuators are used for valves that require multiple rotations of the valve stem to open or close fully, such as gate valves and globe valves. These actuators are capable of providing high torque over a long stroke length. In a power generation plant, multi - turn electric valve actuators are commonly used to control the flow of steam in boiler feedwater systems. The slow and precise operation of these actuators is essential for maintaining the proper pressure and flow of steam, which directly impacts the efficiency of the power generation process.
- They typically use a motor - driven worm gear or a helical gear mechanism to convert the rotational motion of the motor into the linear or multi - turn motion required to operate the valve. Multi - turn actuators often have built - in limit switches to prevent over - travel of the valve stem, protecting the valve and the actuator from damage. Additionally, they may be equipped with torque sensors to monitor the force applied to the valve, ensuring that the valve operates within safe and efficient parameters.
Linear Electric Valve Actuators
- Linear actuators produce a straight - line motion to operate valves. They are used for valves that require linear movement, such as diaphragm valves and some types of pinch valves. In a water treatment plant, linear electric valve actuators can be used to control the dosage of chemicals into the water treatment process. The linear motion of the actuator allows for precise control of the valve opening, ensuring the correct amount of chemicals are added to the water for effective treatment.
- These actuators can be powered by electric motors with a screw - nut mechanism or by solenoids. In the case of motor - driven linear actuators, the motor rotates a screw, and the nut attached to the valve stem moves linearly along the screw as the motor turns. Solenoid - operated linear actuators, on the other hand, use an electromagnetic field to move a plunger, which is connected to the valve stem. Linear actuators are known for their simplicity, reliability, and ability to provide high thrust forces for applications where large - scale fluid control is necessary.
How Electric Valve Actuators Work
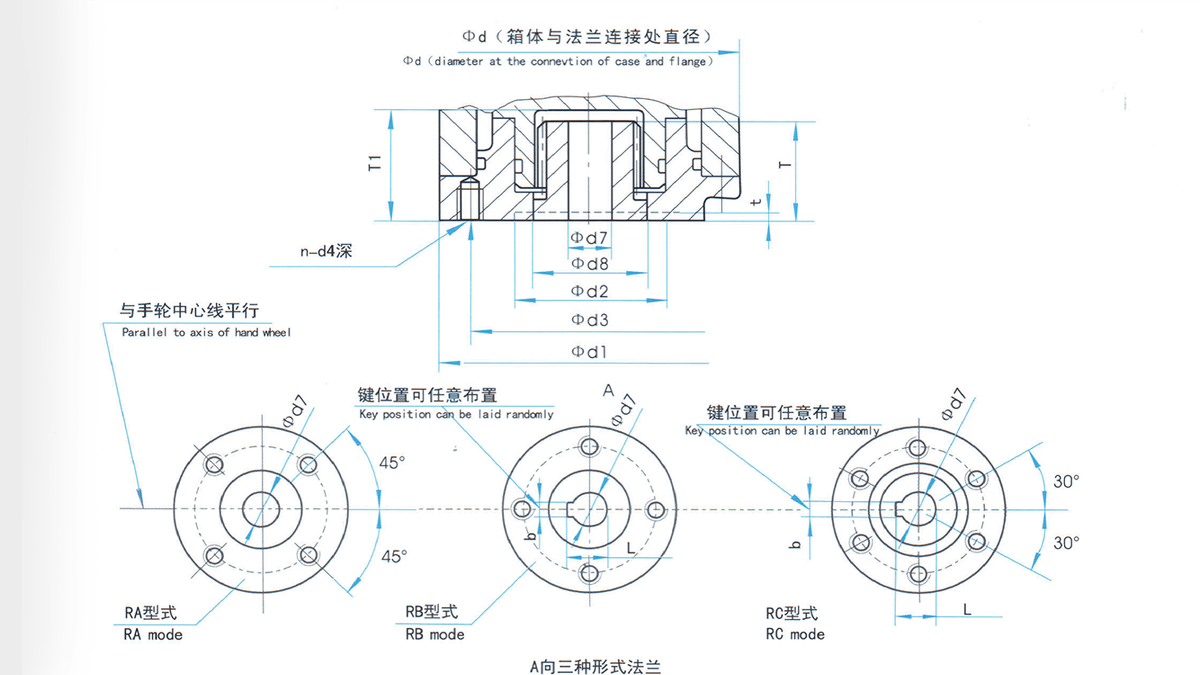
Basic Working Principle
At the core of an electric valve actuator is an electric motor. When an electrical control signal is received, the motor is energized. The motor's rotational motion is then transmitted through a series of mechanical components, such as gears, shafts, and linkages, to the valve stem. The design of these mechanical components depends on the type of actuator (part - turn, multi - turn, or linear) and the specific requirements of the valve it is operating.
For example, in a part - turn electric valve actuator for a butterfly valve, the motor rotates a gearbox, which in turn rotates the shaft of the butterfly valve. The control signal can be adjusted to vary the speed and position of the motor, allowing for precise control of the valve's opening angle. In a multi - turn actuator for a gate valve, the motor drives a worm gear or a helical gear, which converts the high - speed, low - torque output of the motor into the low - speed, high - torque motion required to move the gate valve's stem through multiple turns.
Control Signals and Communication Protocols
Analog Control Signals
- One of the most common types of control signals for electric valve actuators is the analog signal. The most widely used analog control signals are 4 - 20 mA (milliamperes) and 0 - 10 V (volts). In a 4 - 20 mA system, a control system sends an electrical current signal to the actuator. A 4 mA signal typically represents the minimum position of the valve (fully closed in most cases), while a 20 mA signal represents the maximum position (fully open). The actuator adjusts the valve position proportionally to the current value between 4 and 20 mA. For instance, in a heating, ventilation, and air - conditioning (HVAC) system, the temperature sensor sends a signal to the controller, which then outputs a 4 - 20 mA signal to the electric valve actuator controlling the flow of hot water or chilled water. The actuator adjusts the valve position to maintain the desired temperature in the building.
- Similarly, in a 0 - 10 V control system, the voltage level sent by the control system determines the valve position. A 0 V signal may indicate the closed position, and a 10 V signal indicates the open position, with intermediate voltage levels corresponding to intermediate valve positions. Analog control signals are relatively simple and widely used, but they have limitations in terms of accuracy and the ability to transmit additional information.
Digital Control Signals and Communication Protocols
- With the advancement of technology, digital control signals and communication protocols are becoming increasingly popular for electric valve actuators. Some of the commonly used digital communication protocols include Modbus, Profibus, and Ethernet/IP. Modbus is a serial communication protocol that allows for the exchange of data between different devices, such as the control system and the electric valve actuator. It enables the control system to send commands to the actuator, such as opening or closing the valve, and also receive feedback information, such as the valve position, actuator status, and diagnostic data. For example, in a large industrial plant with multiple electric valve actuators, a Modbus - based system can be used to centralize the control and monitoring of all the actuators. The control system can communicate with each actuator over a Modbus network, reducing the complexity of wiring and improving the overall efficiency of the system.
- Profibus is another widely used fieldbus protocol in industrial automation. It offers high - speed communication and reliable data transfer, making it suitable for applications where real - time control and monitoring are crucial. Ethernet/IP, as the name implies, uses Ethernet technology for communication. It provides high - bandwidth communication capabilities, allowing for the transfer of large amounts of data, including video and audio in some advanced applications. Ethernet/IP - enabled electric valve actuators can be easily integrated into enterprise - level networks, enabling seamless communication between the plant floor and higher - level management systems. This integration allows for better optimization of plant operations, as managers can access real - time data on valve performance and make informed decisions.
Key Components of Electric Valve Actuators
Electric Motors
Types of Electric Motors Used in Actuators
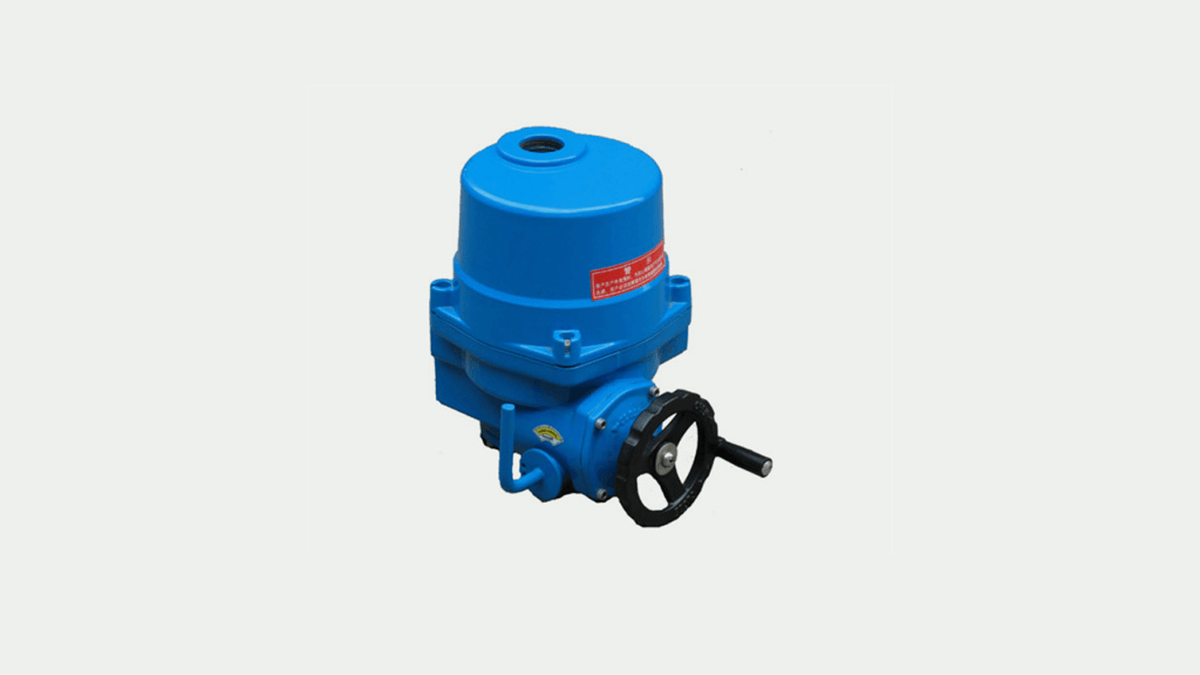
- AC Motors: Alternating current (AC) motors are commonly used in electric valve actuators. Single - phase AC motors are often used for smaller - sized actuators, such as those used in residential or small - commercial applications. They are relatively simple and cost - effective. For example, in a home HVAC system, a single - phase AC motor may be used in the electric valve actuator that controls the flow of refrigerant in the air - conditioning unit. Three - phase AC motors, on the other hand, are used for larger - scale industrial applications where higher power and torque are required. In an oil refinery, three - phase AC motors power the electric valve actuators that control the flow of crude oil and refined products through pipelines. Three - phase motors offer higher efficiency and better starting torque compared to single - phase motors.
- DC Motors: Direct current (DC) motors are also used in some electric valve actuators, especially in applications where precise speed control and smooth operation are required. DC motors can be powered by batteries or a DC power supply. In some mobile or off - grid applications, such as in a remote water pumping station powered by solar panels, DC motors may be used in the electric valve actuators. The use of DC motors allows for easy integration with other DC - powered components in the system. Additionally, DC motors can be controlled more precisely using pulse - width modulation (PWM) techniques, which can adjust the speed and torque of the motor by varying the width of the electrical pulses applied to the motor.
Motor Characteristics and Selection Criteria
- When selecting an electric motor for an electric valve actuator, several factors need to be considered. The torque requirement is a crucial factor. The motor must be able to provide sufficient torque to overcome the forces acting on the valve, such as the pressure of the fluid, the friction in the valve stem, and any external loads. For example, if a valve is used in a high - pressure pipeline, the electric motor in the actuator must have a high - torque rating to ensure that it can open and close the valve smoothly. The speed of the motor is also important. The motor's speed should be appropriate for the application, ensuring that the valve can be opened or closed within the required time. In some applications, such as in a fire - protection system, the valves need to be opened very quickly, so a high - speed motor may be required.
- Efficiency is another important consideration. A more efficient motor will consume less energy, reducing operating costs. Motors with high - efficiency ratings, such as those meeting the Energy Star or IE (International Efficiency) standards, are often preferred. Additionally, the motor's durability and reliability are crucial, especially in industrial applications where the actuator may operate continuously for long periods. Motors with robust construction, high - quality bearings, and proper insulation are more likely to withstand harsh operating conditions and have a longer service life.
Gearboxes and Transmission Systems
Function of Gearboxes in Electric Valve Actuators
- Gearboxes play a vital role in electric valve actuators by converting the high - speed, low - torque output of the electric motor into the low - speed, high - torque motion required to operate the valve. They provide a mechanical advantage, allowing the motor to generate the necessary force to move the valve stem. In a part - turn electric valve actuator, for example, a gearbox may be used to reduce the rotational speed of the motor and increase the torque. This is important because the valve may require a significant amount of torque to rotate through the 90 - degree angle, especially if it is a large - diameter valve or if it is operating under high - pressure conditions.
- In a multi - turn electric valve actuator, the gearbox is used to convert the high - speed rotation of the motor into the slow, multi - turn motion of the valve stem. The gear ratio of the gearbox determines the relationship between the motor speed and the valve stem speed. A higher gear ratio will result in a slower valve stem speed but a higher torque output. Gearboxes also help to protect the motor from overloading. If the valve encounters a high - resistance force, such as when it is stuck or if there is a blockage in the pipeline, the gearbox can absorb some of the shock and prevent the motor from being damaged.
Types of Gearboxes and Transmission Systems
- Worm Gearboxes: Worm gearboxes are commonly used in electric valve actuators, especially in multi - turn applications. They consist of a worm (a screw - like gear) and a worm wheel. The worm rotates the worm wheel, providing a high gear reduction ratio. Worm gearboxes are known for their compact size, high torque transmission capabilities, and self - locking feature. The self - locking feature means that the worm wheel cannot back - drive the worm, which is useful in applications where the valve needs to be held in a particular position without the need for additional braking mechanisms. For example, in a water supply system, a multi - turn electric valve actuator with a worm gearbox can be used to control the flow of water in a pipeline. The self - locking feature of the worm gearbox ensures that the valve remains in the set position even if there are fluctuations in the water pressure.
- Helical Gearboxes: Helical gearboxes use helical - cut gears, which offer several advantages over straight - cut gears. Helical gears have a smoother and quieter operation compared to straight - cut gears because the teeth engage gradually. They also have a higher load - carrying capacity and can transmit more power. In an industrial plant where there are multiple electric valve actuators operating in a noisy environment, helical gearboxes can help to reduce the overall noise level. Helical gearboxes are often used in applications where high - speed and high - torque requirements need to be met, such as in large - scale manufacturing processes where the flow of raw materials and finished products is controlled by valves.
- Planetary Gearboxes: Planetary gearboxes are another type of gearbox used in electric valve actuators. They consist of a central sun gear, multiple planet gears that orbit around the sun gear, and a ring gear. Planetary gearboxes are known for their high efficiency, compact size, and high torque density. They can provide a wide range of gear ratios and are suitable for applications where space is limited but high - torque performance is required. In a robotics - based industrial application, where electric valve actuators are used to control the movement of fluid - filled robotic arms, planetary gearboxes can be used to ensure precise and efficient operation of the valves. The compact size of the planetary gearbox allows for easy integration into the robotic arm design.
Position Sensors and Feedback Systems
Importance of Position Sensors in Electric Valve Actuators
- Position sensors are essential components in electric valve actuators as they provide feedback to the control system about the actual position of the valve. This feedback is crucial for accurate control and monitoring of the valve's operation. Without position sensors, the control system would not know whether the valve has reached the desired position or if it is stuck in an intermediate position. In a chemical processing plant, for example, the accurate position of the valves is critical to ensure the proper mixing and flow of chemicals. If a valve is not fully open or closed as required, it can lead to incorrect chemical reactions, product quality issues, and even safety hazards.
- Position sensors also play a role in preventive maintenance. By continuously monitoring the valve position, the control system can detect any abnormal behavior, such as the valve taking longer than usual to reach the desired position or oscillating around a certain position. These anomalies can be early indicators of problems with the valve, actuator, or the pipeline, allowing maintenance personnel to take corrective action before a major failure occurs.
Types of Position Sensors Used
- Potentiometers: Potentiometers are one of the simplest types of position sensors used in electric valve actuators. They work based on the principle of variable resistance. As the valve stem moves, it rotates a wiper on a resistive element, changing the resistance value. The control system measures this resistance value and converts it into a position signal. Potentiometers are relatively inexpensive and easy to install. However, they have limitations in terms of accuracy and durability. The resistive element can wear out over time, affecting the accuracy of the position measurement. In a residential HVAC system, potentiometers may be used in the electric valve actuators to control the flow of air or water. The relatively low - cost and simple operation of potentiometers make them suitable for this type of application where high - precision position sensing may not be as critical.
- Hall Effect Sensors: Hall effect sensors are non - contact sensors that detect the position of a magnetic field. In an electric valve actuator, a magnet is attached to the valve stem, and the Hall effect sensor is mounted in a fixed position. As the valve stem moves, the magnetic field around the sensor changes, and the sensor outputs a voltage signal proportional to the position of the magnet. Hall effect sensors are more accurate and reliable than potentiometers as they have no moving parts in contact with the sensing element. They are also less affected by environmental factors such as dust, dirt, and moisture. In an oil and gas pipeline system, where the actuators are often exposed to harsh outdoor conditions, Hall effect sensors are commonly used to ensure accurate and reliable valve position sensing.Encoder Sensors: Encoder sensors are highly accurate position sensors that can provide both absolute and incremental position information. Absolute encoders can determine the exact position of the valve stem at any given time, regardless of the actuator's history. Incremental encoders, on the other hand, measure the change in position from a reference point. Encoder sensors use optical or magnetic technologies to generate digital signals that represent the position of the valve stem. They are often used in applications where very high - precision control is required, such as in semiconductor manufacturing plants. In these plants, the flow of ultra - pure gases and liquids needs to be controlled with extreme accuracy, and encoder - based position sensors in the electric valve actuators can ensure that the valves are positioned precisely to meet the strict process requirements.
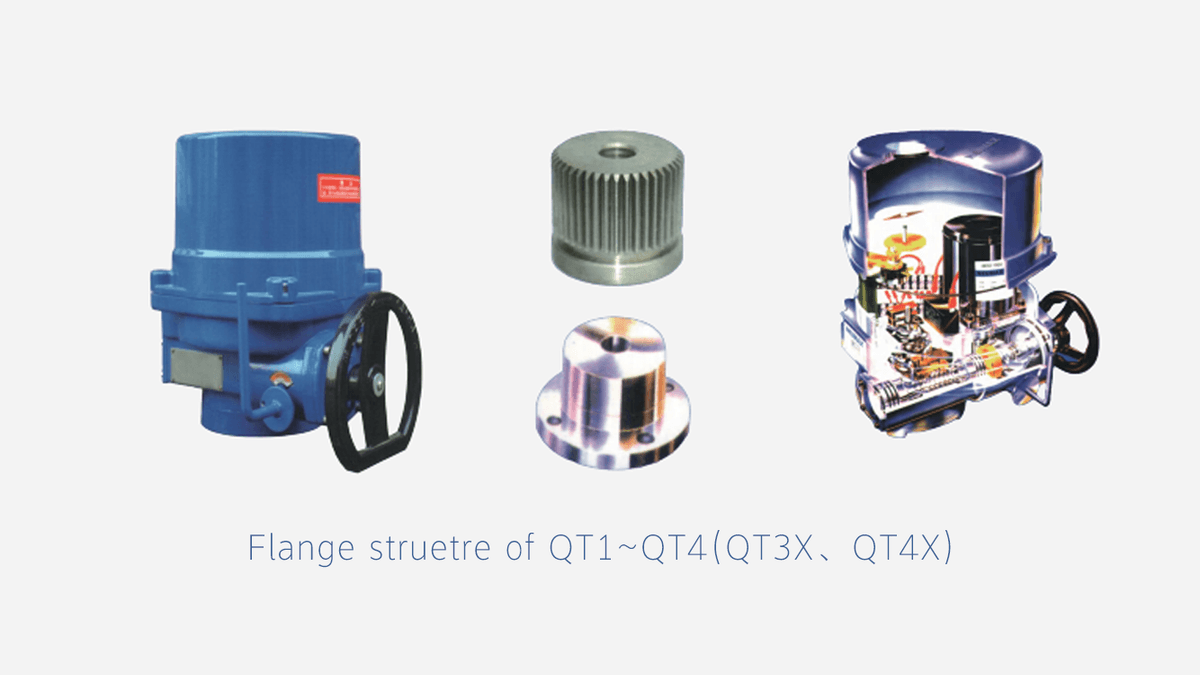
Applications of Electric Valve Actuators
Power Generation (Continued)
In a coal - fired power plant, electric valve actuators are also crucial for managing the steam cycle. They control the flow of steam from the boiler to the turbine, ensuring that the turbine operates at optimal efficiency. By precisely adjusting the position of the valves, these actuators help regulate the steam pressure and flow rate, which directly impacts the power output of the plant. In addition, they are used in the cooling water systems to control the flow of water for condensing the steam back into water, completing the cycle.
In a nuclear power plant, electric valve actuators play an even more critical role in safety - related systems. They are used to control the flow of coolant in the reactor core, ensuring that the core remains at a safe temperature. Any malfunction in these actuators could potentially lead to a dangerous situation, so high - reliability and redundant designs are often employed. For example, in the emergency core cooling system, multiple electric valve actuators work in tandem to ensure that in the event of an emergency, coolant can be quickly and accurately directed to the reactor core to prevent overheating.
Water Supply and Distribution
Electric valve actuators are used in water treatment plants and water distribution networks to control the flow of water. In a water treatment plant, they are used to control the dosage of chemicals such as chlorine for disinfection, flocculants for sediment removal, and pH - adjusting agents. Precise control of these chemical dosages is crucial for producing clean and safe drinking water.
In the water distribution network, electric valve actuators are used to control the flow of water in pipelines, regulate water pressure, and isolate sections of the network for maintenance or emergency repairs. For example, in a large - scale urban water distribution system, electric valve actuators are installed at key points in the network to ensure that water is distributed evenly and that pressure is maintained within acceptable limits. They can also be used to quickly shut off the water supply in the event of a pipeline break or other emergency, minimizing water loss and potential damage.
Fluid Characteristics
The characteristics of the fluid being controlled are one of the most important factors in selecting an electric valve actuator. The type of fluid (e.g., water, gas, oil, or chemical), its temperature, pressure, viscosity, and corrosiveness all need to be considered. For example, if the fluid is highly corrosive, such as in a chemical processing application involving acids or alkalis, the actuator materials must be resistant to corrosion. Stainless steel, Hastelloy, or other specialty alloys may be required for the actuator components in contact with the fluid.
In addition, the temperature and pressure of the fluid can affect the selection of the actuator. High - temperature applications may require actuators with heat - resistant materials and seals, while high - pressure applications need actuators that can withstand the pressure without leakage or failure. For a high - pressure natural gas pipeline, the electric valve actuator must be designed to handle the high pressure of the gas, typically several hundred pounds per square inch (psi) or more.
Valve Type and Size
The type and size of the valve being operated also play a significant role in actuator selection. Different valve types (e.g., ball valves, butterfly valves, gate valves, globe valves) have different torque requirements for opening and closing. Part - turn valves like ball valves and butterfly valves generally require less torque compared to multi - turn valves such as gate valves and globe valves. Therefore, the actuator must be able to provide the appropriate torque to operate the valve smoothly.
The size of the valve, measured by its diameter, also affects the torque requirement. Larger - diameter valves typically require more torque to operate. For example, a 12 - inch diameter gate valve will require a much more powerful actuator compared to a 2 - inch diameter gate valve. In addition to torque, the stroke length (for multi - turn and linear valves) and the angular rotation (for part - turn valves) need to be considered to ensure that the actuator can fully open and close the valve within the required time.
Performance Requirements
Torque and Thrust
As mentioned earlier, the torque or thrust capacity of the electric valve actuator is a critical performance parameter. The actuator must be able to generate sufficient torque or thrust to overcome the forces acting on the valve, including the fluid pressure, friction in the valve stem, and any external loads. When selecting an actuator, it is important to calculate the maximum torque or thrust required under normal operating conditions and also consider any peak loads that may occur during start - up, shut - down, or in the event of a blockage.
For example, in a high - pressure steam application, the actuator may need to overcome the high - pressure steam pushing against the valve disc, as well as the friction in the valve seat and stem. An actuator with a torque rating that is too low may not be able to open or close the valve, leading to operational problems and potential safety hazards. Therefore, it is essential to select an actuator with a torque or thrust capacity that has a sufficient margin of safety.
Speed and Response Time
The speed at which the electric valve actuator can open or close the valve is another important consideration, especially in applications where rapid response is required. In a fire - protection system, for example, the valves need to be opened quickly to release fire - suppressing agents. Similarly, in some industrial processes, such as in a chemical plant where a sudden change in process conditions requires immediate adjustment of the valve position, a fast - responding actuator is necessary.
The response time of the actuator, which is the time it takes for the actuator to start moving after receiving a control signal, also affects the overall performance of the system. Actuators with shorter response times can provide more precise control and better system stability. However, increasing the speed and reducing the response time may come at the cost of higher energy consumption and potentially reduced lifespan of the actuator components. Therefore, a balance needs to be struck based on the specific application requirements.
Market Trends and Future Outlook of Electric Valve Actuators
Increasing Demand for Energy - Efficient Actuators
With the growing focus on energy conservation and sustainability, there is an increasing demand for energy - efficient electric valve actuators. Actuators with high - efficiency motors, such as those using brushless DC motors or high - efficiency AC motors, are becoming more popular. These motors consume less energy, resulting in lower operating costs for end - users.
In addition, energy - saving features such as variable - speed control and intelligent control algorithms are being incorporated into electric valve actuators. For example, in an HVAC system, an electric valve actuator with variable - speed control can adjust the flow of fluid based on the actual load, reducing energy consumption compared to a fixed - speed actuator. The demand for energy - efficient actuators is expected to continue to grow as more industries and countries implement stricter energy - efficiency regulations.
Advancements in Digitalization and Smart Actuators
The trend towards digitalization is also having a significant impact on the electric valve actuator market. Smart electric valve actuators, which are equipped with advanced sensors, communication capabilities, and embedded intelligence, are becoming increasingly popular. These actuators can provide real - time data on their performance, such as valve position, torque, temperature, and vibration.
This data can be used for predictive maintenance, allowing maintenance personnel to detect potential problems before they occur and schedule maintenance activities more effectively. Smart actuators can also be integrated into industrial Internet of Things (IIoT) platforms, enabling seamless communication with other devices and systems in the plant. For example, in a smart factory, electric valve actuators can communicate with other production equipment, sensors, and control systems to optimize the overall production process.
In conclusion, electric valve actuators are essential components in awide range of industrial, commercial, and residential applications. Their proper selection, installation, and maintenance are crucial for ensuring reliable operation and optimal performance. As market trends continue to evolve and new technologies emerge, electric valve actuators will continue to play an increasingly important role in various industries, driving innovation and efficiency.
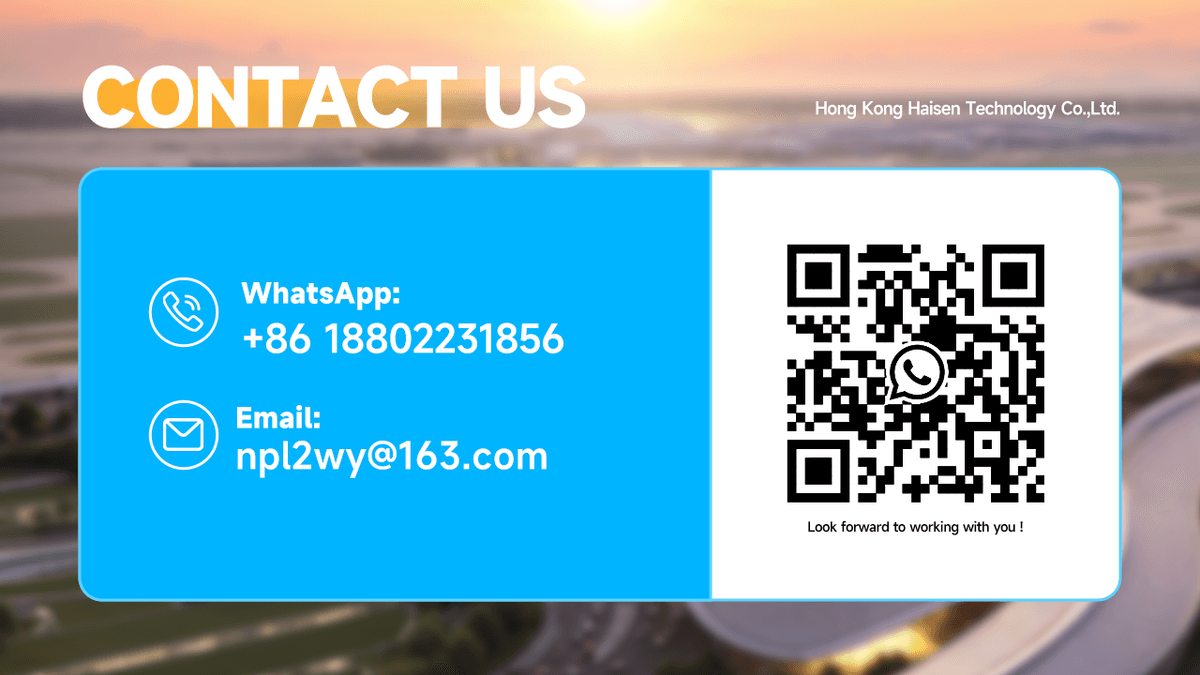