Electric valve actuators are the backbone of modern industrial automation, enabling precise, efficient control of valve operations in countless critical processes. From regulating fluid flow in pipelines to managing complex industrial systems, electric valve actuators have revolutionized how industries approach valve control—replacing manual labor with automated precision and reliability. In this comprehensive guide, we’ll explore everything you need to know about electric valve actuators: what they are, how they work, their key benefits, types, applications, how to choose the right one, installation and maintenance best practices, top brands, future trends, and more. Whether you’re an industry professional seeking to upgrade your systems or a newcomer looking to understand these essential devices, this guide will equip you with the knowledge to make informed decisions—and ensure your operations run smoother, safer, and more efficiently with electric valve actuators.
What Are Electric Valve Actuators?
At their core, electric valve actuators are motorized devices designed to automate the opening, closing, and positioning of valves in industrial systems. Powered by electricity, these actuators eliminate the need for manual valve operation, allowing for remote or local control with unparalleled precision. Electric valve actuators are engineered to convert electrical energy into mechanical motion, driving valve stems to adjust flow rates of liquids, gases, or slurries in pipelines and processes.
What sets electric valve actuators apart from traditional pneumatic or hydraulic actuators is their reliance on electric motors—rather than compressed air or hydraulic fluid—to generate motion. This dependence on electricity makes electric valve actuators highly versatile, as they can integrate seamlessly with modern control systems, sensors, and smart technology. Electric valve actuators are celebrated for their accuracy, repeatability, and durability, making them indispensable in industries where even minor deviations in flow control can lead to costly errors, safety risks, or process inefficiencies.
In short, electric valve actuators are more than just “automated valve openers”—they are critical components that ensure industrial processes operate at peak performance, with minimal human intervention and maximum reliability.
How Do Electric Valve Actuators Work?
Understanding the mechanics of electric valve actuators is key to appreciating their precision and efficiency. At a basic level, electric valve actuators follow a simple process: they receive an electrical signal, convert that signal into mechanical motion, and use that motion to adjust the valve’s position. Let’s break this down step by step:
- Receiving the Signal: Electric valve actuators are connected to a control system (either local or remote), which sends an electrical signal (typically 4-20 mA, 0-10 VDC, or digital commands like Modbus) indicating the desired valve position (e.g., “open 50%” or “close fully”).
- Converting Electrical Energy to Motion: Inside the actuator, an electric motor (AC or DC) activates upon receiving the signal. This motor drives a gear train or screw mechanism, which amplifies the motor’s torque to generate enough force to move the valve stem.
- Adjusting the Valve: The gear or screw mechanism translates the motor’s rotational motion into linear or rotational movement of the valve stem. For example, in a ball valve, the actuator’s rotation (usually 90°) turns the ball to open or close the flow path; in a gate valve, linear motion lifts or lowers the gate to regulate flow.
- Feedback Loop: Many modern electric valve actuators include position sensors (e.g., potentiometers or encoders) that send real-time feedback to the control system, confirming the valve has reached the desired position. This closed-loop system ensures accuracy and allows for immediate corrections if deviations occur.
The simplicity of this process—coupled with advancements in motor technology and gear design—makes electric valve actuators highly efficient. Unlike pneumatic actuators, which rely on consistent air pressure, or hydraulic actuators, which require fluid lines, electric valve actuators operate with minimal auxiliary equipment, reducing complexity and potential points of failure. This reliability is why electric valve actuators are preferred in remote or hard-to-reach locations, where maintaining pneumatic or hydraulic systems would be impractical.
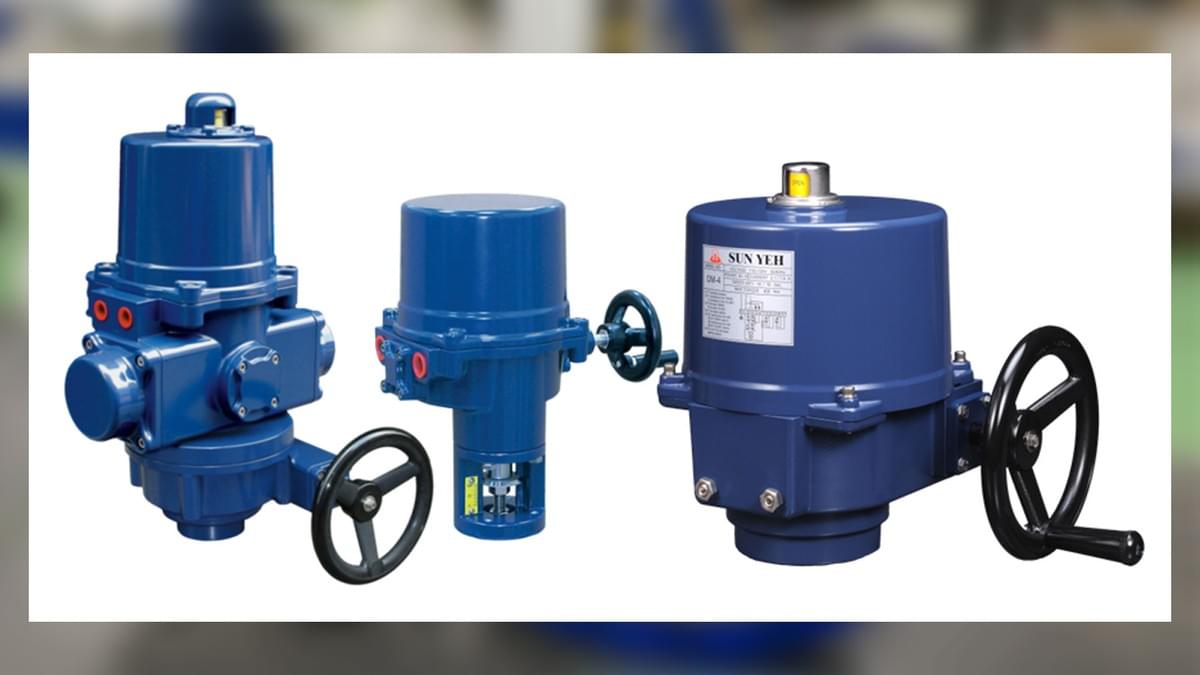
Types of Electric Valve Actuators
Electric valve actuators come in several types, each designed to match the specific needs of different valve designs and industrial applications. The two primary categories are quarter-turn electric valve actuators and multi-turn electric valve actuators, with variations tailored to specialized use cases.
1. Quarter-Turn Electric Valve Actuators
Quarter-turn electric valve actuators are engineered for valves that require a 90° rotation to open or close fully. These include ball valves, butterfly valves, and plug valves—common in industries where quick, on/off or throttling control is needed.
- How They Work: Quarter-turn electric valve actuators use a motor and gear system to rotate the valve stem exactly 90° (or a portion thereof for partial opening). This rotational motion aligns the valve’s internal components (e.g., a ball with a bore or a butterfly disc) to allow or block flow.
- Key Advantages:
- Fast operation: Quarter-turn movements are quicker than multi-turn adjustments, making them ideal for applications requiring rapid response (e.g., emergency shutoffs).
- Compact design: Their simple gear trains make them smaller and lighter than multi-turn actuators, saving space in tight installations.
- Cost-effectiveness: Less complex mechanics reduce manufacturing costs, making them a budget-friendly option for high-volume applications.
- Common Applications: Water treatment plants (controlling water flow), chemical processing (regulating chemical transfers), and HVAC systems (adjusting airflow in commercial buildings).
2. Multi-Turn Electric Valve Actuators
Multi-turn electric valve actuators are designed for valves that require multiple rotations (often 10+ turns) to open or close fully. These include gate valves, globe valves, and pinch valves—used in applications where precise, gradual flow control is critical.
- How They Work: Multi-turn electric valve actuators use a motor paired with a screw or worm gear system, which converts rotational motion into linear movement over multiple turns. This slow, steady motion allows for fine-tuning of flow rates (e.g., opening a gate valve 10% for low flow or 90% for high flow).
- Key Advantages:
- Exceptional precision: Multi-turn adjustments enable minute positioning, essential in industries like oil refining or pharmaceutical manufacturing, where flow rates must be exact.
- High torque output: The gear systems amplify torque, making them suitable for large, high-pressure valves that require significant force to operate.
- Durability: Robust construction withstands continuous use in demanding environments (e.g., high temperatures or corrosive atmospheres).
- Common Applications: Oil and gas pipelines (controlling crude oil flow), power generation (regulating steam flow in turbines), and pharmaceutical production (managing precise ingredient dosing).
3. Specialized Electric Valve Actuators
Beyond the two main types, there are specialized electric valve actuators designed for niche applications:
- Linear Electric Valve Actuators: These convert rotational motor motion into linear movement (e.g., pushing or pulling a valve stem) and are used with globe valves or diaphragm valves.
- Spring-Return Electric Valve Actuators: These include a spring mechanism that returns the valve to a “fail-safe” position (open or closed) if power is lost, critical in safety-critical applications like gas pipelines.
- Smart Electric Valve Actuators: Integrated with sensors, IoT connectivity, and diagnostic software, these actuators offer remote monitoring, predictive maintenance alerts, and data logging—ideal for Industry 4.0 environments.
Benefits of Electric Valve Actuators
Electric valve actuators offer a host of advantages over traditional pneumatic, hydraulic, or manual valve control systems. These benefits make them the preferred choice for modern industrial automation, driving efficiency, safety, and cost savings across sectors.
1. Unmatched Precision and Accuracy
Electric valve actuators deliver precise control over valve positioning, with repeatability often within 0.1% of the desired position. This level of accuracy is critical in industries where flow rates directly impact product quality or process safety. For example:
- In pharmaceutical manufacturing, electric valve actuators ensure exact dosing of active ingredients, preventing over- or under-dosing that could render medications ineffective or unsafe.
- In food processing, they regulate the flow of ingredients (e.g., sugar or flavorings) to maintain consistent product taste and texture.
Unlike pneumatic actuators, which can suffer from pressure fluctuations that cause imprecise movements, electric valve actuators rely on steady electrical signals, ensuring consistent performance even in dynamic conditions.
2. Reduced Manual Labor and Costs
By automating valve operations, electric valve actuators eliminate the need for manual valve turning—saving time, reducing labor costs, and minimizing human error. In large industrial facilities (e.g., refineries or water treatment plants), valves may be located in hazardous or hard-to-reach areas (e.g., high platforms, confined spaces, or toxic environments). Manual operation in these settings risks worker safety and is inefficient.
Electric valve actuators allow operators to control valves remotely via a control panel, SCADA system, or even a smartphone app, reducing the need for on-site personnel. Over time, this translates to significant labor savings: a single operator can monitor and adjust dozens of valves simultaneously, whereas manual control might require a team of workers.
3. Enhanced Monitoring and Feedback
Modern electric valve actuators are equipped with sensors that provide real-time data on valve position, motor temperature, torque output, and energy consumption. This feedback is transmitted to control systems, giving operators full visibility into system performance. For example:
- If a valve is stuck, the actuator will alert operators to the issue, allowing for timely repairs before a process shutdown occurs.
- Energy consumption data helps identify inefficient actuators, enabling proactive upgrades to reduce utility costs.
This level of monitoring is impossible with manual valves and far more limited with pneumatic or hydraulic systems, which lack built-in diagnostic capabilities.
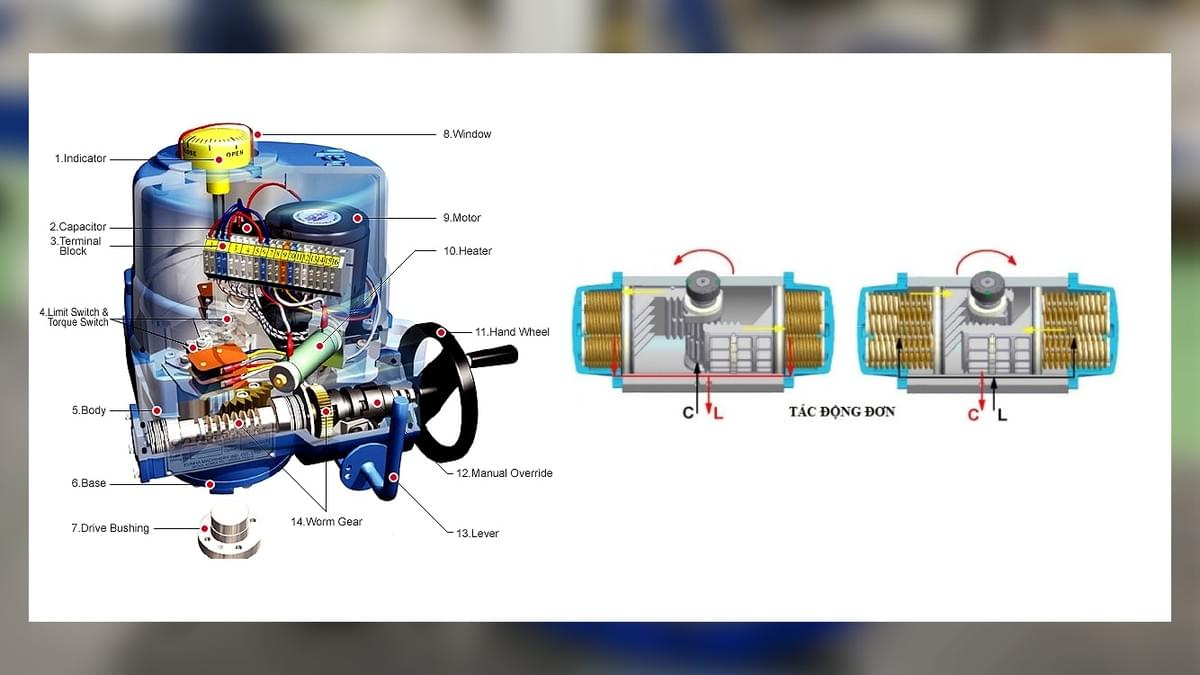
4. Greater Flexibility and Integration
Electric valve actuators are designed to integrate seamlessly with existing industrial systems, including PLCs (Programmable Logic Controllers), DCS (Distributed Control Systems), and IoT platforms. They support a range of communication protocols (e.g., Modbus, Profibus, or Ethernet/IP), making them compatible with both legacy and cutting-edge control systems.
This flexibility allows for easy upgrades: facilities can retrofit electric valve actuators onto existing valves without overhauling their entire control infrastructure. For example, a water treatment plant using manual valves can gradually replace them with electric valve actuators, integrating each new unit into its existing SCADA system for centralized control.
5. Advanced Diagnostic Features
Many electric valve actuators include built-in diagnostic tools that detect potential issues before they cause failures. These features include:
- Overload protection: The actuator shuts down if torque exceeds safe limits, preventing motor burnout or valve damage.
- Temperature monitoring: Alerts operators if the motor overheats, indicating a need for maintenance.
- Fault codes: Specific error messages (e.g., “valve jammed” or “power supply unstable”) simplify troubleshooting, reducing downtime.
Proactive diagnostics minimize unplanned shutdowns—a critical advantage in industries where downtime can cost thousands of dollars per hour (e.g., oil refining or semiconductor manufacturing).
6. Long-Term Cost-Effectiveness
While electric valve actuators may have a higher upfront cost than manual or pneumatic alternatives, their long-term savings outweigh this investment. They require less maintenance than hydraulic systems (which need fluid changes and leak repairs) or pneumatic systems (which require air compressor upkeep). Additionally, their energy efficiency—especially in modern models with low-power motors—reduces electricity costs over time.
Durability is another factor: electric valve actuators are built with robust materials (e.g., stainless steel, aluminum alloys) that withstand harsh conditions, extending their lifespan to 10–20 years with proper maintenance. This longevity reduces replacement costs, making electric valve actuators a cost-effective choice for long-term operations.
Applications of Electric Valve Actuators
Electric valve actuators are used across a wide range of industries, thanks to their versatility, precision, and reliability. Here’s a closer look at how they contribute to key sectors:
1. Petrochemical and Oil & Gas
The petrochemical industry relies on electric valve actuators to control the flow of crude oil, natural gas, and chemical intermediates in refineries, pipelines, and storage facilities. In these high-pressure, high-temperature environments, precision and safety are paramount:
- Multi-turn electric valve actuators regulate flow in pipelines, ensuring steady pressure to prevent leaks or explosions.
- Spring-return electric valve actuators serve as emergency shutoffs, closing valves automatically if a leak or pressure spike is detected.
- Smart electric valve actuators monitor pipeline conditions remotely, allowing operators to adjust flow rates without onsite visits—critical for offshore platforms or remote oil fields.
2. Water and Wastewater Treatment
Water treatment plants use electric valve actuators to manage the flow of raw water, chemicals (e.g., chlorine for disinfection), and treated water. Quarter-turn electric valve actuators are common here, as they quickly open or close butterfly valves to control water distribution:
- In filtration systems, they adjust flow rates to ensure optimal contact time between water and filter media.
- In wastewater treatment, they regulate the flow of sludge and chemicals, ensuring efficient purification before water is released back into the environment.
- Remote control capabilities allow operators to adjust valves during peak demand (e.g., morning water usage spikes) without onsite intervention.
3. Power Generation
Electric valve actuators play a vital role in power plants (fossil fuel, nuclear, and renewable) by controlling steam, water, and fuel flow:
- In coal-fired plants, multi-turn electric valve actuators regulate steam flow to turbines, optimizing energy output.
- In nuclear plants, they control the flow of cooling water, with fail-safe features to prevent overheating in case of power loss.
- In solar thermal plants, they adjust valves to direct heat transfer fluids, maximizing energy capture from sunlight.
4. Food and Beverage Processing
Hygiene and precision are critical in food and beverage production, making electric valve actuators an ideal choice. They control the flow of ingredients, cleaning agents, and finished products:
- Stainless steel electric valve actuators (resistant to corrosion and easy to sanitize) are used in dairy processing to regulate milk flow during pasteurization.
- Quarter-turn actuators adjust butterfly valves in brewing, controlling the flow of wort, yeast, and beer to ensure consistent flavor profiles.
- Modulating electric valve actuators precisely dose additives (e.g., vitamins in juice production), maintaining nutritional accuracy.
5. HVAC and Building Automation
In commercial and industrial buildings, electric valve actuators control airflow and water flow in HVAC systems, maintaining optimal temperature and humidity:
- They adjust damper valves to regulate air flow in office buildings, ensuring even heating or cooling across floors.
- In hospitals, they control the flow of hot water to radiators, preventing temperature fluctuations in patient rooms.
- Smart electric valve actuators integrate with building management systems (BMS), allowing for energy-efficient adjustments based on occupancy or time of day (e.g., reducing heating in empty offices).
6. Metallurgy and Mining
Metallurgical processes (e.g., steel production) and mining operations rely on electric valve actuators to control the flow of molten metals, coolants, and slurry:
- High-temperature electric valve actuators (rated for 200°C+) regulate coolant flow in blast furnaces, preventing overheating.
- In mining, they control the flow of slurry (crushed ore mixed with water) in processing plants, ensuring efficient separation of minerals.
7. Shipbuilding and Marine
On ships and offshore platforms, electric valve actuators manage fuel, water, and waste flow in harsh, corrosive environments:
- Salt-resistant electric valve actuators control ballast water valves, adjusting a ship’s buoyancy for safe navigation.
- They regulate fuel flow to engines, optimizing efficiency during long voyages.
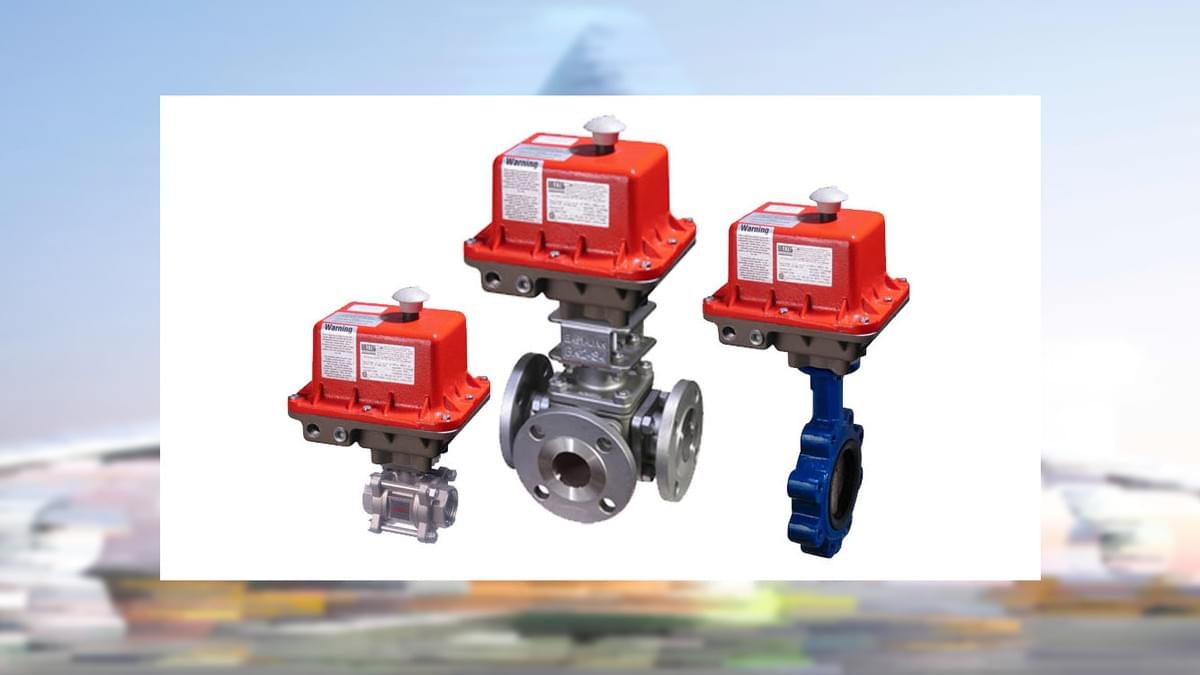
How to Choose the Right Electric Valve Actuators
Selecting the right electric valve actuators for your application requires careful consideration of several key factors. Choosing incorrectly can lead to inefficiency, frequent breakdowns, or safety risks—so take the time to evaluate these criteria:
1. Valve Type and Size
The first step is to match the actuator to the valve it will control. As discussed earlier:
- Quarter-turn electric valve actuators pair with ball, butterfly, or plug valves (90° rotation).
- Multi-turn electric valve actuators work with gate, globe, or pinch valves (multiple rotations).
Additionally, consider the valve’s size (e.g., 2-inch, 6-inch) and weight—larger valves require actuators with higher torque output to operate smoothly.
2. Torque Requirements
Torque is the force needed to turn or move the valve. Undersized torque can cause the actuator to stall or fail; oversized torque may damage the valve. Calculate torque requirements based on:
- Valve size and type: Larger valves or those with tight seals (e.g., gate valves) require more torque.
- Operating pressure: High-pressure systems increase friction between valve components, raising torque needs.
- Media type: Viscous fluids (e.g., sludge) or abrasive materials (e.g., sand) increase resistance, requiring higher torque.
Most manufacturers provide torque charts for their valves—use these to select an actuator with 10–20% more torque than the valve’s maximum requirement to account for wear over time.
3. Speed of Operation
How quickly do you need the valve to open or close?
- Fast-acting applications (e.g., emergency shutoffs) require quarter-turn electric valve actuators with high rotational speed (e.g., 90° in 5 seconds).
- Precision applications (e.g., chemical dosing) may need slower speeds to allow for fine adjustments (e.g., 90° in 30 seconds).
4. Environmental Conditions
Electric valve actuators must withstand the environment where they’ll be installed. Key factors include:
- Temperature: Choose actuators rated for the operating range (e.g., -40°C to 80°C for cold climates; 150°C+ for high-heat applications like refineries).
- Humidity and moisture: Waterproof or explosion-proof enclosures (e.g., NEMA 4X, IP67) are essential for outdoor, wet, or dusty environments.
- Corrosion: Use actuators with stainless steel or epoxy-coated housings in salty (marine) or chemical-rich environments.
- Hazardous areas: In explosive environments (e.g., oil refineries), select ATEX or UL-certified electric valve actuators designed to prevent sparking.
5. Power Supply
Electric valve actuators require a consistent power source. Determine:
- Voltage: Most use AC power (110V, 220V) or DC power (12V, 24V) for remote applications (e.g., solar-powered systems).
- Phase: Single-phase (for small actuators) or three-phase (for high-torque models).
Ensure the installation site has the correct power supply—otherwise, you may need transformers or backup batteries.
6. Control Options
Electric valve actuators offer various control methods; choose one that integrates with your system:
- On/off control: Simple open/close commands (ideal for basic applications like water shutoffs).
- Modulating control: Adjusts valve position incrementally (e.g., 0–100% open) for precise flow control (common in HVAC or chemical processing).
- Proportional control: Uses feedback loops to maintain a setpoint (e.g., keeping pressure constant in a pipeline).
Also, consider communication protocols (e.g., Modbus, Bluetooth) if you need remote monitoring or integration with smart systems.
7. Safety Features
In safety-critical applications, look for electric valve actuators with:
- Fail-safe modes: Spring-return mechanisms that close or open the valve during power loss.
- Overload protection: Shuts down the motor if torque exceeds safe levels.
- Emergency stop buttons: Allows manual override in case of system failure.
8. Maintenance and Support
Choose brands that offer easy access to spare parts, technical support, and user-friendly manuals. This ensures quick repairs and minimizes downtime. For example, Haisen’s QT series includes modular components, making replacement of gears or motors simple.
Top Brands of Electric Valve Actuators
Several leading manufacturers dominate the electric valve actuators market, each offering unique features tailored to specific industries. Here’s an overview of top brands to consider:
1. Rotork
Rotork is a global leader in valve actuation, known for innovative, reliable electric valve actuators. Their IQ series stands out for:
- Smart technology: Integrated IoT connectivity for remote monitoring and control.
- High torque range: From 30 Nm to 10,000 Nm, suitable for large industrial valves.
- Durability: Explosion-proof and weatherproof designs for harsh environments.
Rotork electric valve actuators are popular in oil and gas, water treatment, and power generation.
2. Auma
Auma specializes in robust, high-performance electric valve actuators for heavy-duty applications. Their SA series offers:
- Modular design: Easy to customize with different control options (e.g., manual override, bus communication).
- High precision: Repeatability within 0.5% for critical processes.
- Energy efficiency: Low-power motors reduce operating costs.
Auma electric valve actuators are widely used in mining, metallurgy, and chemical processing.
3. Emerson Electric Co.
Emerson’s Bettis brand is synonymous with innovation in electric valve actuators. Their EIM series features:
- Advanced diagnostics: Real-time data on valve performance and predictive maintenance alerts.
- Compact size: Ideal for space-constrained installations (e.g., offshore platforms).
- Seamless integration: Compatible with Emerson’s DeltaV DCS for centralized control.
Emerson electric valve actuators excel in pharmaceutical, food, and beverage industries.
4. Haisen
Haisen is a rising star in the electric valve actuators market, with their QT series part-turn actuators gaining traction for:
- Versatility: Controls butterfly, ball, and plug valves in industries like petrochemicals, shipbuilding, and food processing.
- Local/remote operation: Flexible control options for both on-site and off-site adjustments.
- Durability: Withstands extreme temperatures and corrosive media, making it ideal for harsh environments.
Haisen electric valve actuators offer a balance of performance and affordability, appealing to small and large facilities alike.
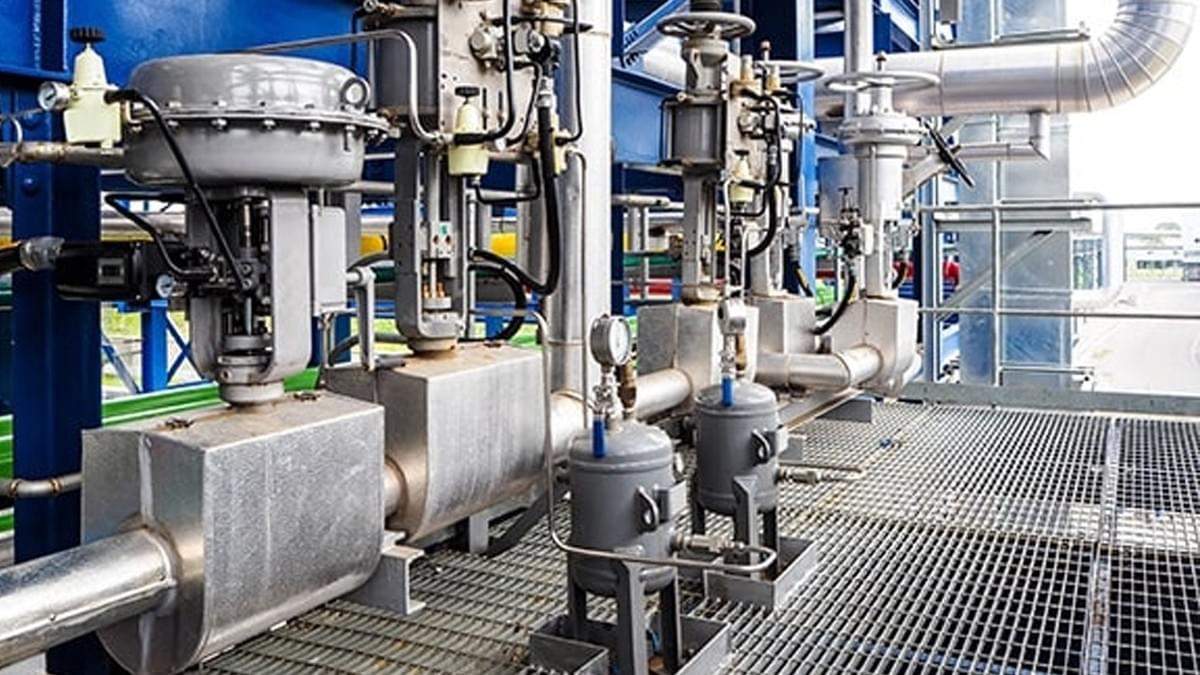
Installation and Maintenance of Electric Valve Actuators
Proper installation and regular maintenance are critical to ensuring electric valve actuators perform reliably and last for years. Here’s a step-by-step guide:
Installation Best Practices
- Prepare the Site: Ensure the valve is properly mounted and aligned before attaching the actuator. Misalignment can cause excess wear on gears and motor.
- Mount the Actuator: Secure the actuator to the valve using manufacturer-supplied hardware. Tighten bolts evenly to prevent distortion.
- Connect Electrical Wiring: Follow the wiring diagram in the user manual to connect power and control signals. Use waterproof connectors in wet environments.
- Calibrate the Actuator: Test the actuator’s movement to ensure it aligns with the valve’s open/closed positions. Adjust limit switches if necessary to prevent over-rotation.
- Test Operation: Run a full cycle (open to close) to verify smooth movement and correct feedback to the control system.
Maintenance Tips
- Regular Inspections: Check for signs of wear, corrosion, or loose parts monthly. Pay special attention to gears, wiring, and seals.
- Lubrication: Apply manufacturer-recommended lubricant to moving parts (gears, shafts) every 6–12 months to reduce friction.
- Cleaning: Remove dirt, dust, or debris from the actuator’s exterior and vents to prevent overheating. Use a soft brush or compressed air—avoid water in non-waterproof models.
- Electrical Checks: Inspect wiring and connectors for corrosion or damage quarterly. Tighten loose connections and replace damaged wires.
- Functional Testing: Test the actuator’s response to control signals and emergency features (e.g., fail-safe mode) semi-annually to ensure reliability.
By following these steps, you can extend the lifespan of your electric valve actuators and minimize unexpected failures.
Troubleshooting Common Issues with Electric Valve Actuators
Even with proper maintenance, electric valve actuators may encounter issues. Here’s how to diagnose and resolve common problems:
1. Actuator Fails to Respond
- Possible Causes: Power supply failure, loose wiring, or a faulty control signal.
- Solution: Check if the actuator is receiving power (use a multimeter). Inspect wiring for breaks or loose connections. Test the control signal with a signal generator to ensure it’s within the actuator’s range.
2. Valve Moves Sluggishly
- Possible Causes: Low torque, lubrication issues, or a jammed valve.
- Solution: Verify the actuator’s torque rating matches the valve’s requirements. Check for worn gears or insufficient lubrication. Inspect the valve for debris or corrosion that may be causing jams.
3. Overheating Motor
- Possible Causes: Overloading, poor ventilation, or a failing motor.
- Solution: Reduce torque demands by checking for valve obstructions. Clean vents to improve airflow. If the motor continues to overheat, replace it with a higher-rated model.
4. Incorrect Position Feedback
- Possible Causes: Misaligned sensors or faulty position encoders.
- Solution: Recalibrate the position sensor according to the manufacturer’s instructions. Replace damaged encoders if necessary.
Future Trends in Electric Valve Actuators
As industries embrace automation and sustainability, electric valve actuators are evolving to meet new demands. Here are the key trends shaping their future:
1. Smart Technology Integration
The rise of Industry 4.0 is driving the development of “smart” electric valve actuators, equipped with:
- IoT connectivity: Real-time data transmission to cloud platforms for remote monitoring.
- AI-powered diagnostics: Machine learning algorithms that predict failures based on performance trends (e.g., detecting abnormal torque patterns that signal a future jam).
- Predictive maintenance: Alerts that notify operators of upcoming service needs (e.g., “lubrication required in 100 hours”), reducing downtime.
2. Energy Efficiency
With a focus on sustainability, manufacturers are designing electric valve actuators with:
- Low-power motors: Brushless DC motors that consume up to 30% less energy than traditional models.
- Energy recovery systems: Capturing kinetic energy during valve closing to recharge batteries in remote applications.
3. Eco-Friendly Materials
To reduce environmental impact, electric valve actuators are using:
- Recyclable materials: Aluminum and stainless steel components that are easy to recycle at end-of-life.
- Low-VOC coatings: Non-toxic paints and finishes that reduce harmful emissions during manufacturing.
4. Increased Customization
As industries demand tailored solutions, manufacturers are offering more customizable electric valve actuators, with options for:
- Custom torque ratings and speeds.
- Specialized enclosures for unique environments (e.g., extreme cold or radiation).
- Branded control interfaces that integrate with proprietary systems.
Conclusion
Electric valve actuators are transforming industrial automation, offering precision, efficiency, and reliability that manual or traditional actuators can’t match. From petrochemical plants to food processing facilities, they play a critical role in ensuring safe, efficient operations—reducing costs, minimizing human error, and enabling seamless integration with modern control systems.
By understanding their types, benefits, applications, and how to choose, install, and maintain them, you can select the perfect electric valve actuators for your needs. As technology advances, these devices will only become more intelligent, energy-efficient, and versatile—making them an investment that will drive industrial progress for years to come.
Ready to upgrade your operations with electric valve actuators? Contact a trusted manufacturer today to discuss your specific requirements and find the ideal solution for your facility.
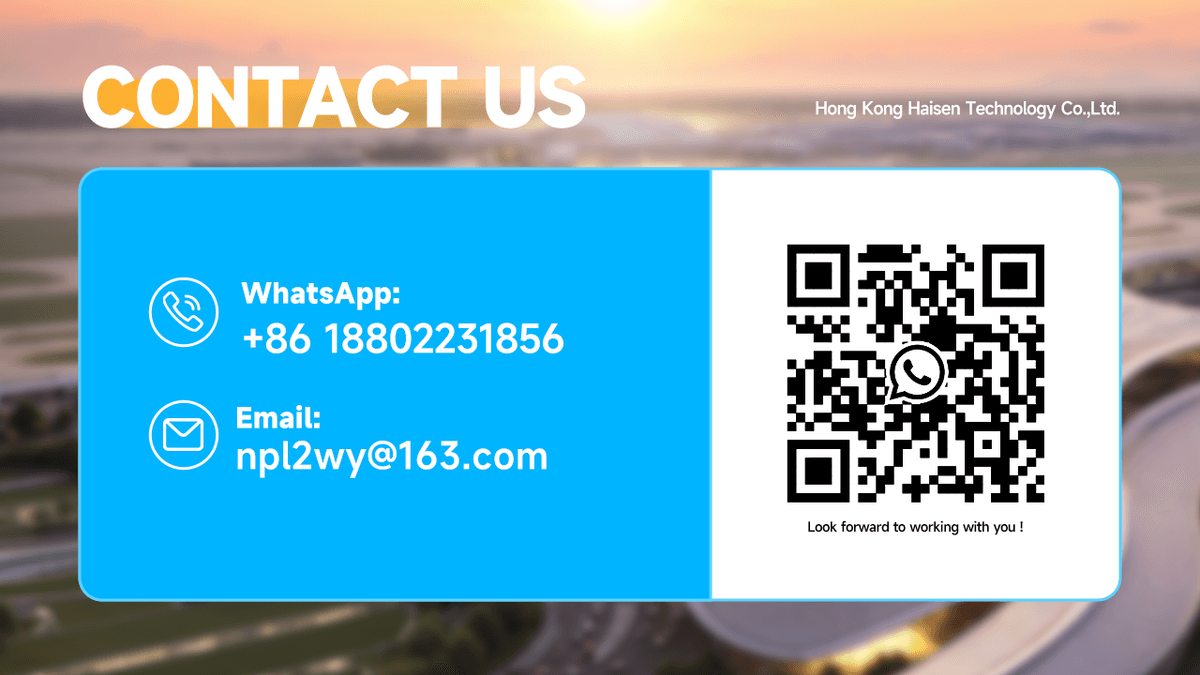